Plastic Welding Techniques: Achieving Strong, Durable Bonds in Fabrication
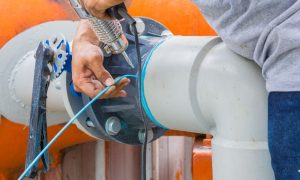
In our continued quest to provide top-quality plastic products to clients in the Ottawa area, we understand that the strength and durability of a fabricated component are crucial to its overall performance. Among the myriad of available bonding methods, plastic welding offers a time-tested and versatile solution for creating strong, lasting connections between plastic materials. This advanced technique is employed across a wide range of industries and applications, including COVID-19 countermeasures, safety and security products, marketing and display cases, podiums, election boxes, windshields, tables, and benches.
Plastic welding is a fabrication process in which heat and/or pressure are used to fuse thermoplastic materials together, resulting in a strong, cohesive bond. The right welding technique can significantly impact the quality and longevity of the finished product, making it essential to select the most suitable method for each unique project requirement. As plastic fabrication experts, we are dedicated to guiding clients through the process of choosing and implementing the ideal plastic welding solutions for their specific needs, ensuring optimal product performance and durability.
In this comprehensive blog post, we will explore the fascinating world of plastic welding, delving into the various techniques available and their respective benefits, challenges, and applications. Furthermore, we will discuss essential factors to consider when selecting a plastic welding method and provide valuable tips for ensuring successful bonding outcomes. Join us on this engaging journey as we unlock the potential of plastic welding and its critical role in achieving strong, durable bonds in the plastic fabrication process.
Overview of Plastic Welding Techniques
Numerous plastic welding techniques are available, each with its unique advantages, challenges, and ideal applications. Some of the most common techniques in the plastic fabrication industry include:
- Hot Gas Welding: This method involves directing a stream of heated gas, typically air or nitrogen, over the surfaces of the plastic materials to be joined. Once the surfaces have reached a molten state, a filler rod made of the same material is added to the joint and fused to both parts, forming a strong bond upon cooling. Hot gas welding is effective for joining materials such as PVC, polyethylene, and polypropylene.
- Ultrasonic Welding: Ultrasonic welding utilizes high-frequency vibrations to generate heat through friction between the plastic components being bonded. This technique is particularly suitable for smaller assemblies and thin materials and is commonly used in the medical, automotive, and consumer electronics industries.
- Laser Welding: Using a focused laser beam to generate localized heat, this non-contact method allows for precise, controlled melting and fusion of plastic materials. Laser welding is ideal for applications requiring a high level of accuracy, such as medical devices and automotive components.
- Friction Welding: In friction welding, pressure and rotational movement are applied to the surfaces of the plastic materials being joined, generating heat through friction. Once a molten state is reached, the parts are pressed together, forming a strong bond as the materials cool and solidify. This technique is often employed in the aerospace and automotive industries.
Factors to Consider When Choosing a Welding Technique
Selecting the most suitable plastic welding technique for a specific application involves careful consideration of various factors, including:
- Material Compatibility: Assess the properties of the plastic materials being bonded, ensuring that they are compatible with the chosen welding method and can form a strong, lasting bond.
- Application Requirements: Consider the unique requirements of the individual application, such as joint strength, aesthetics, and production speed. Select a welding technique that best aligns with these objectives and contributes to a successful outcome.
- Equipment and Cost: Evaluate the necessary equipment and cost implications associated with each welding technique, taking into consideration factors such as complexity, maintenance, and energy consumption.
- Production Volume and Scale: Assess the production volume and scale of the project, ensuring that the welding technique can accommodate the desired production output while maintaining efficiency and product quality.
Tips for Successful Plastic Welding Outcomes
To ensure optimal results when utilizing plastic welding techniques, follow these best practices:
- Surface Preparation: Clean and prepare the surfaces of the plastic materials to be welded, removing any contaminants that could compromise the bond strength. Proper surface preparation promotes strong, reliable bonds between the materials.
- Skilled Personnel: Ensure that technicians and operators are experienced and skilled in the chosen welding technique, fostering a high level of consistency and success within the fabrication process.
- Equipment Maintenance and Calibration: Regularly maintain and calibrate welding equipment to maintain optimal performance, and follow the manufacturer’s recommendations for upkeep and maintenance schedules.
- Quality Control and Testing: Implement comprehensive quality control measures, including visual inspections and mechanical testing, to ensure that the welded joints meet project specifications and requirements.
Innovative Applications of Plastic Welding Techniques
Plastic welding techniques have been embraced by various industries due to their ability to produce strong, durable bonds while maintaining versatility and efficiency. Here are some notable applications of plastic welding in diverse sectors:
- Medical Devices: Many medical devices, such as IV bags, syringes, and diagnostic equipment, rely on plastic welding for their assembly. Techniques such as ultrasonic and laser welding provide the precision and cleanliness necessary for these critical instruments.
- Automotive Components: Plastic welding is widely used in the assembly of interior and exterior automotive components, such as bumpers, instrument panels, and lighting housings, ensuring a robust, durable bond that can withstand the rigors of daily vehicle use.
- Consumer Electronics: Welding techniques like ultrasonic and laser welding are employed in the fabrication of various electronic devices, such as smartphones, tablets, and household appliances, providing secure, reliable bonds and preserving the aesthetic appeal of the product.
Harness the Power of Plastic Welding for Your Fabrication Projects
Plastic welding is a robust, versatile, and effective solution for achieving strong, durable bonds within the plastic fabrication process. By understanding the distinct techniques available and recognizing the critical factors to consider when selecting a suitable method, you can confidently approach your plastic welding endeavors with success.
Our team of experienced plastic welders in Ottawa from Canus Plastics Inc. is committed to providing expert guidance and support for all your plastic welding needs, helping to ensure a high level of performance and durability in the final product. Contact us today to learn more about how we can assist you in achieving optimal results with your plastic welding projects.