A Simple Guide to Our Welding Techniques and Their Uses
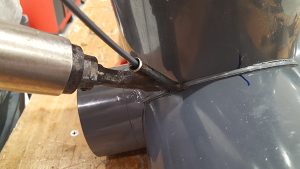
At Canus Plastics Inc., we understand the importance of robust and precise techniques in the creation of plastic products. Welding, especially tailored for plastics, plays a pivotal role in ensuring the structural integrity and longevity of the items we manufacture. This process is integral not only in producing everyday items but also in creating specialized products that meet the diverse needs of our clients, spanning from safety barriers to intricate marketing display cases.
Welding is more than just fusing materials; it’s a meticulous science that involves various sophisticated techniques adapted to suit different types of plastics and product requirements. Each technique brings distinct advantages to the table, whether it’s enhancing the visual appeal of the final product or ensuring resistance to environmental stressors. By incorporating advanced welding methods, we provide customized solutions that align perfectly with our clients’ specifications.
Safety is also paramount in every aspect of our operations. As we continually adapt to the latest advancements in welding technology, we also rigorously apply industry-leading safety measures to protect our team and guarantee the highest quality in our manufacturing processes. This commitment not only helps us maintain our high standards but also fosters innovation, driving forward the future of plastic manufacturing.
What Is Welding and Why Do We Use It in Plastic Manufacturing?
At Canus Plastics Inc., we employ welding as a core process in plastic manufacturing due to its efficiency and the strong, durable bonds it creates. Plastic welding involves the use of heat and pressure to fuse two plastic materials together, forming a permanent bond that enhances the structural integrity of the final product. This method is indispensable because it allows for the construction of complex structures that meet the high standards required in many industries, including medical, automotive, and construction.
Why welding? The reason is straightforward. This technique provides a cohesive connection without the need for additional fastening materials, such as bolts or adhesives, which can weaken the structural strength of plastic parts. Welding also allows for smoother and cleaner product finishes, which are crucial in applications where aesthetics are as important as functionality. Whether ensuring smooth surfaces for healthcare equipment or secure joints in protective barriers, welding helps us meet diverse customer requirements with precision and reliability.
Different Welding Techniques and Their Specific Applications
Our approach at Canus Plastics Inc. is tailored to optimize for different scenarios, employing a variety of welding techniques based on the specific requirements of the product and its application. Here are a few methods we regularly use:
- Hot Plate Welding: This process is excellent for larger or irregularly shaped components. It utilizes a heated plate to melt plastic surfaces before they are pressed together to form a bond. We typically use this technique for items that require a strong, hermetic seal, such as tanks and fittings.
- Ultrasonic Welding: Ideal for small or delicate parts, ultrasonic welding uses high-frequency vibrations to generate heat through friction, joining the pieces effectively without damaging the component’s integrity. Its applications include automotive components like instrument panels and medical devices, for which precision is paramount.
- Spin Welding: This technique involves rotating one plastic part against a stationary part at high speed. The resulting friction melts the contact surfaces, forming a durable joint once cooled. Commonly, we employ spin welding for circular components, such as nozzles and valves, where a tight, leak-proof seal is necessary.
Choosing the right welding technique allows us to address the unique challenges posed by different projects. Whether it’s ensuring ultra-clean joins for medical devices or achieving strong, resilient bonds for automotive applications, our expertise in various welding methods ensures we deliver products that not only meet but exceed our clients’ expectations.
Safety Measures and Best Practices in Welding
At Canus Plastics Inc., ensuring the safety of our team and the integrity of our products during the welding process is paramount. We adhere to rigorous safety measures and industry best practices to guarantee that every project is completed without incident and to the highest quality. Our welders are equipped with state-of-the-art personal protective equipment (PPE), including helmets with visors for eye protection, heat-resistant gloves, and aprons that safeguard against sparks and high temperatures. These measures prevent workplace injuries and ensure that our staff can operate in secure and controlled environments.
In addition to personal safety gear, we implement comprehensive training programs that keep our team updated on the latest welding techniques and safety protocols. Each welder at Canus Plastics Inc. is certified and receives continuous education to deepen their knowledge and skill set. This education covers the handling of different materials and the appropriate welding techniques to apply, which varies depending on the project’s specific needs. Our emphasis on safety and education helps maintain a safe workspace, ensuring that we deliver products that meet our high standards and the expectations of our clients.
Future Trends and Innovations in Welding Technology
In the evolving field of welding, staying ahead of technological advancements is crucial for maintaining the quality and competitiveness of our manufacturing processes. At Canus Plastics Inc., we are always looking towards the future, integrating new technologies that enhance the efficiency and precision of our welding techniques. One emerging trend is the use of automated welding systems, which offer remarkable consistency and speed, particularly for large-scale production runs. These robotic systems are programmed to perform complex welds with precision, reducing the likelihood of human error and optimizing material usage.
Another promising innovation is the development of new welding materials and methods that provide stronger bonds and greater resistance to wear and environmental factors. These advances enable us to explore new applications for welded plastic components, expanding our ability to serve diverse industries with more sophisticated and durable products. By embracing these technologies, we enhance our capability to deliver custom-tailored solutions that meet the evolving needs of our clients while adhering to our commitment to quality and innovation.
Conclusion
At Canus Plastics Inc., our dedication to mastering welding technology and its applications in plastic manufacturing underpins our commitment to excellence and innovation. By prioritizing safety, embracing continuous learning, and integrating cutting-edge welding technologies, we ensure our products are not only effective but also superior in quality and durability. Our focus on maintaining a highly skilled team and incorporating advanced materials and technologies allows us to meet the diverse and demanding requirements of our clients, reinforcing our position as a leader in the plastic manufacturing industry.
For those seeking high-quality, custom-made plastic products built to precise specifications and safety standards, turn to Canus Plastics Inc. Our plastic manufacturing company is here to meet your needs with expertise, reliability, and an unwavering commitment to excellence. Contact us today to learn how we can assist in bringing your project to fruition with the highest level of professionalism and quality assurance.