How to Use Vacuum Forming for Custom Parts
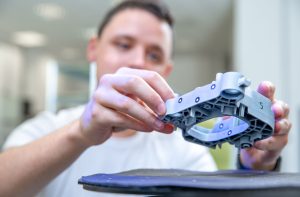
Plastic vacuum forming is like the magic wand of the manufacturing world. It takes something everyday, like a flat piece of plastic, and transforms it into a wide variety of useful custom parts. This process is all about heating a plastic sheet and shaping it around a mold. From automotive parts to medical devices, vacuum forming finds applications in many fields. It’s a simple yet effective way to produce custom parts that are not only cost-effective but also quick to produce.
In Ottawa, the demand for these custom parts continues to rise across various industries. Businesses are constantly seeking out reliable methods to get quality parts without breaking the bank. That’s where vacuum forming steps up. It offers an excellent solution for creating detailed and robust pieces. Whether it’s for prototyping or large-scale production, vacuum forming makes it easier for industries to meet their needs efficiently.
Why Choose Vacuum Forming for Custom Parts
Vacuum forming stands out due to its versatility and ability to adapt to different needs. It’s the go-to method for businesses looking to produce custom parts that need specific shapes and dimensions. Here’s why it’s such a great choice:
– Adaptability: Whether you need a small-scale prototype or a larger product run, vacuum forming can handle it. The process easily adapts to the project’s size, allowing for both flexibility and precision.
– Cost-Effectiveness: Cost is a big deal for most companies. Vacuum forming is more wallet-friendly than many other manufacturing techniques. It reduces material waste and shortens production time, which helps in saving money.
– Detail and Complexity: The process can produce parts with intricate designs and fine details. This ability makes it ideal for products that require high-quality standards, such as medical devices or intricate automotive panels.
Imagine needing a custom plastic cover for a piece of lab equipment. With vacuum forming, you can achieve the exact dimensions and features required. This method ensures that even complex designs are attainable with great accuracy, enhancing the functionality and aesthetics of the final product. So, whether it’s for prototyping or full-scale production, vacuum forming is a method worthy of consideration due to these benefits.
Key Steps in Vacuum Forming Process
Understanding the basic steps in vacuum forming can help you appreciate how this versatile method brings designs to life. Here’s a quick look at how it works:
1. Designing the Mold: This step involves creating a mold that matches the desired shape of your custom part. Careful planning at this stage is crucial, as the mold will determine the final design.
2. Heating the Plastic: The plastic sheet is heated until it’s soft and pliable. Keeping an eye on temperature control during this phase is important to ensure the material forms perfectly over the mold.
3. Forming: Once the plastic is heated, it is placed over the mold while a vacuum pulls it into place, ensuring a snug fit. The vacuum helps the plastic conform to all the details of the mold, capturing intricate textures and shapes.
4. Cooling: After the plastic cools and hardens, the newly formed part is removed from the mold, ready for any additional processing or finishing touches.
Using quality materials is key to a successful vacuum forming process. Common choices include ABS, Polycarbonate, and Polystyrene due to their durability and ease of use. By following these steps, you can produce high-quality custom parts that meet your specific requirements.
Applications of Vacuum Formed Custom Parts
Vacuum formed parts are a cornerstone in many industries, thanks to their practicality and versatility. These custom parts find applications in various fields, providing effective solutions to unique challenges.
– Automotive Industry: Here, vacuum forming serves in creating parts like dashboards, bumpers, and door panels. The process ensures that each component fits OEM specifications and maintains the desired aesthetic.
– Health Sector: Medical devices and equipment often make use of vacuum forming for parts that require precision and sterility. Think of trays, housings, and other containment solutions.
– Point-of-Sale Displays: Retailers often choose vacuum formed parts for their visual displays. Its flexibility allows design freedom while ensuring durability for frequent use.
Consider how local Ottawa businesses, such as cafes and shops, use creatively designed display units to showcase their products. Vacuum forming enables these businesses to have customized fixtures that are both eye-catching and functional.
Benefits of Using Professional Services for Vacuum Forming
Partnering with experts for your vacuum forming needs can greatly enhance the quality and efficiency of your projects. Professional services leverage state-of-the-art technology and extensive expertise to deliver top-notch results.
– Precision and Quality: Experts ensure each part meets exact specifications, maintaining high standards of quality throughout the process.
– Advanced Technology: They utilize cutting-edge equipment and techniques that boost production efficiency and output quality.
– Satisfaction and Timeliness: With experienced professionals on your side, expect smooth operations and timely delivery of your custom parts.
When you leave it to the pros, you free yourself from worrying about the technical details, focusing instead on using these superior products to achieve business success. Taking advantage of professional services ensures your parts not only look good but also perform exceptionally well, keeping your operations running smoothly.
Crafting Your Ideal Custom Parts with Vacuum Forming
Vacuum forming offers a blend of adaptability, cost-effectiveness, and precision that is hard to match by other manufacturing processes. Choosing this method can empower businesses in Ottawa and beyond to create reliable, high-quality custom components that suit their specific demands.
When considering the vast possibilities vacuum forming provides, whether for an initial prototype or bulk production, it’s clear that professional involvement magnifies these benefits. Embracing this approach means equipping your business with uniquely crafted solutions that not only solve problems but also push the boundaries of innovation and design.
Considering all the benefits vacuum forming can bring your business, it’s time to see how this technology can meet your unique needs. Learn more about how we can help with your plastic vacuum forming projects by exploring the innovative solutions offered by Canus Plastics Inc. Your next custom part could be just a click away.