Troubleshooting Thermoforming Defects and Their Prevention
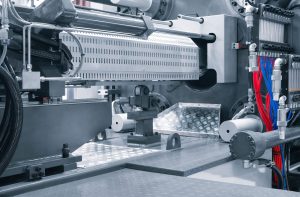
Thermoforming is an important process in making plastic products, allowing manufacturers to create diverse and complex shapes by heating and molding plastic sheets. This method is especially valued for its efficiency and flexibility in production. By harnessing the heat and pressure, it opens up possibilities in design that cater to various industries, from packaging to automotive components.
However, unexpected defects in the thermoforming process can cause disruptions, impacting the operation and the quality of the final products. Recognizing these common defects is vital to maintaining smooth production and ensuring products meet quality standards. This article aims to highlight the typical issues that can arise during thermoforming and shares practical strategies to prevent them, ensuring that the process runs smoothly.
Common Thermoforming Defects
Thermoforming, despite its versatility, isn’t without its challenges. Several common defects can disrupt the manufacturing process, and understanding them is the first step towards prevention. Let’s explore a few prevalent issues:
– Warping: One of the more visible issues, warping occurs when the plastic cools unevenly. This can lead to deformations in the final product, affecting its aesthetic and functional qualities.
– Bubbles: This defect manifests as trapped air within the plastic. Bubbles compromise the integrity of the product, often leading to weak spots or breakages.
– Thickness Inconsistencies: Variations in the thickness of the final product can arise from improper material distribution during forming. This inconsistency can cause reliability issues in use.
– Surface Imperfections: These can be minor or major flaws, like scratches or burn marks, usually appearing due to contaminated molds or incorrect temperature settings.
Each of these defects can greatly impact both the efficacy of the manufacturing process and the quality of the end product. They can result in wasted materials and time, leading to increased costs and delayed projects. Identifying and understanding these defects ensures that manufacturers can take proactive steps in enhancing their production lines.
Identifying Causes of Defects
Exploring the causes of these defects helps paint a clearer picture of thermoforming challenges. Here are some key reasons these issues might occur:
– Incorrect Temperature Settings: The wrong temperature can affect plastic malleability. Too hot or too cold, and you risk problems like bubbles or warping. It’s essential to get the heat just right.
– Material Issues: Low-quality or incompatible materials can cause defects. Not all plastics are suitable for every thermoforming process, and choosing the right kind is fundamental.
– Machine Malfunctions: Worn or improperly calibrated machines can result in uneven pressure application or temperature fluctuations, leading to a host of defects.
Troubleshooting these origins involves closely examining each aspect of the process, from machine settings to material quality. Regular checks and balances ensure that issues are caught early before they develop into larger problems. By understanding where things can go awry, manufacturers are better equipped to maintain a flawless operation.
In production, think of it like baking a cake. If the oven isn’t set correctly or the ingredients aren’t right, the result won’t be what you intended. Similarly, careful attention in thermoforming is required to ensure quality and efficiency.
Prevention Strategies
Ensuring that thermoforming runs smoothly starts with understanding and applying effective prevention strategies. The key here is to set the right conditions for your plastics and machinery. Here are some core strategies you can implement:
– Optimal Temperature Settings: Always calibrate your equipment to maintain consistent temperatures. Thermoplastic sheets require specific heat levels to become pliable without degrading. Monitor temperatures closely to avoid problems like warping and bubbles.
– Regular Maintenance and Calibration: Keeping machines well-maintained is crucial. Regular servicing and calibration prevent unexpected breakdowns and ensure that all components function correctly. Even a minor glitch can result in defects during production.
– High-Quality Materials: Use materials that match the specific demands of your project. Choosing high-grade plastics consistent in composition and thickness reduces the risk of defects. Consistent quality leads to reliable outputs.
Imagine a craftsman maintaining his tools. Sharp, well-cared-for tools create better results than neglected ones. Similarly, every aspect of your thermoforming setup demands attention, ensuring that the final product meets all expectations and needs.
Leveraging Professional Help
Even with preventive measures in place, expertise from industry professionals can enhance production quality. Professionals can offer insights and services that elevate your thermoforming processes. They have the experience to troubleshoot efficiently, quickly identifying issues that may not be apparent. Here’s why considering professional help could be beneficial:
– Access to Expertise: Industry pros have encountered various scenarios and bring a wealth of knowledge to tackle unique challenges.
– Advanced Equipment: Professionals often have access to the latest technology and tools that can be too expensive or complex for internal setups.
– Efficient Solutions: By leveraging their experience, pros can diagnose problems with precision, reducing downtime and avoiding costly trial-and-error approaches.
In conclusion, getting outside help ensures smoother operations and enhances product quality. It’s a bit like having a seasoned guide on a hiking trip; they know the terrain and can help steer you clear of any pitfalls.
Maintain Seamless Thermoforming Practices
Addressing defects in thermoforming requires a mix of good practice, regular maintenance, and expert advice. By identifying common problems, understanding their origins, and using effective prevention strategies, you can greatly improve the efficiency of your processes. Ensuring high standards and consistent results involves attention to both the materials and machinery.
Moreover, reaching out for professional assistance when needed ensures that your production remains on track. Skilled professionals can offer the right tools and strategies to keep your operation running smoothly and error-free.
A well-executed thermoforming process leads to high-quality products that meet both market needs and customer expectations. This clear and deliberate approach ensures your production stays efficient, reliable, and responsive to changing demands.
For those looking to optimize their operations with precision and reliability, turning to experts can make a significant difference. If you need guidance or support with plastic for thermoforming, trust the expertise of Canus Plastics Inc. We’re here to help you navigate challenges and achieve impeccable results with your thermoforming processes.