How Vacuum Forming Transforms Plastic Sheets
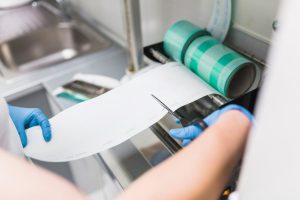
Vacuum forming is a unique process that turns flat plastic sheets into three-dimensional objects using heat and suction. This method is widely used in various industries because it is cost-effective and versatile. If you’ve ever seen plastic packaging or custom plastic parts, there’s a good chance that vacuum forming was used to create them.
The vacuum forming process starts with a sheet of plastic that is heated until it becomes soft and pliable. Then, the plastic is stretched over a mould and a vacuum is used to suck the air out, forcing the plastic to take the shape of the mould. Once the plastic cools and hardens, it retains this new shape. This simple yet effective method allows for the production of a wide variety of plastic products, from protective covers to retail displays.
Understanding how vacuum forming works and its benefits can help you see why it’s such a popular choice for creating plastic parts and products. In this article, we’ll explore what vacuum forming is, walk through the process step-by-step, look at its many applications, and explain why we should be your go-to supplier for vacuum formed products.
What is Vacuum Forming?
Vacuum forming is a type of thermoforming. It’s a process that uses heat and suction to shape plastic sheets into three-dimensional objects. The plastic sheet is first heated until it’s soft and flexible. Once pliable, the sheet is placed over a mould, and a vacuum is applied to suck the air out and pull the plastic tightly around the mould.
This method is popular because it’s simple and cost-effective. It can produce large and small items, making it great for various applications. From packaging to automotive parts, vacuum forming is a versatile way to create custom plastic components. The process is also relatively quick, which helps in producing items faster compared to other methods.
One of the main advantages of vacuum forming is its ability to create detailed shapes with fine contours. It can handle a variety of plastic materials, including ABS, polycarbonate, and acrylic, giving manufacturers flexibility in choosing the right material for the job. The ability to reproduce intricate designs accurately makes vacuum forming a preferred method for many industries.
The Vacuum Forming Process Step-by-Step
Here’s a step-by-step look at how vacuum forming works:
1. Heating the Plastic: A flat plastic sheet is placed into a frame and then heated to a specific temperature. The sheet becomes soft and flexible, ready to be shaped.
2. Positioning the Mould: Once the plastic is heated, it’s moved to the moulding station. The mould, usually placed on a platen, rises to meet the heated plastic sheet.
3. Applying the Vacuum: The vacuum pump is activated to suck the air out from between the plastic sheet and the mould. This pulls the plastic tightly around the mould, making it take the exact shape of the mould.
4. Cooling and Releasing: After the plastic has been formed around the mould, it needs to cool down. Fans or other cooling methods are often used to speed up this process. Once cooled, the plastic retains its new shape and is removed from the mould.
5. Trimming and Finishing: The formed plastic piece usually has extra material around the edges. This excess is trimmed off to give the product its final shape. Additional finishing touches might include drilling holes, polishing, or adding other features.
This straightforward process allows for quick production while maintaining high-quality standards. Each step is crucial for ensuring the final product meets the desired specifications.
Applications of Vacuum Forming in Plastic Products
Vacuum forming has a wide range of applications because it is so versatile. It can be used to create products in many different industries, ensuring a high level of customization and precision. Here are some common applications:
1. Packaging
– Blister Packs: These are often used to hold products securely while showing them off to customers.
– Clamshell Packaging: This type of packaging is used for various consumer goods, providing both protection and visibility.
2. Automotive
– Interior Panels: Vacuum forming is used to create dashboard components and door panels with intricate designs.
– Protective Covers: These are used to shield various car parts from damage.
3. Medical Devices
– Housings and Enclosures: These protect medical equipment while keeping it lightweight and durable.
– Trays and Organizers: Used for storing surgical instruments and other medical tools.
4. Retail Displays
– Point of Purchase Displays: Custom displays that attract attention to products in stores.
– Signage: Lightweight and durable signs that can be easily installed or relocated.
5. Household Products
– Storage Bins: Sturdy bins for organizing household items.
– Custom Containers: These can be made in various shapes and sizes for specific uses.
The versatility of vacuum forming proves its value in numerous fields, providing effective solutions tailored to different needs. Each application benefits from the precision, efficiency, and customizability that vacuum forming offers.
Why Choose Canus Plastics Inc. for Vacuum Forming
Choosing the right company for vacuum forming is crucial to ensuring you get high-quality products. We offer several advantages that set us apart:
1. Advanced Technology: We use state-of-the-art vacuum forming equipment to ensure precision and quality. Our machines are capable of handling different types of plastic and creating detailed designs.
2. Experienced Team: Our team has extensive experience in vacuum forming and plastic manufacturing. We understand the intricacies of the process and can tackle even the most challenging projects.
3. Custom Solutions: We offer tailored solutions to meet your specific needs. Whether you need a unique shape, size, or design, we work closely with you to bring your vision to life.
4. Quality Assurance: We are committed to maintaining high-quality standards throughout the production process. From the initial design to the final product, we ensure that every step meets our rigorous quality checks.
5. Wide Range of Products: We provide an extensive array of plastic products, including COVID-19 countermeasures, safety and security items, marketing and display cases, podiums, election boxes, windshields, tables, and benches. This variety means you can find all your plastic needs under one roof.
Conclusion
Vacuum forming transforms flat plastic sheets into various three-dimensional objects using a simple and effective process. This method is versatile, cost-effective, and allows for creating detailed and custom designs. Whether for packaging, automotive parts, medical devices, retail displays, or household items, vacuum forming delivers high-quality products designed to meet specific needs.
For top-notch vacuum forming services, Canus Plastics Inc. stands out with its advanced technology, experienced team, and commitment to quality. We offer custom solutions and a wide range of products to cater to different industries. Reach out to Canus Plastics Inc. today to discover how we can help with your vacuum forming needs. Let us transform your ideas into reality!