Vacuum Forming: An Efficient Solution for Plastic Manufacturing
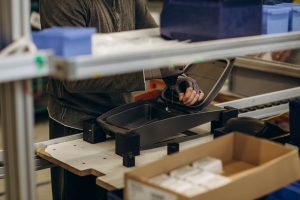
In the ever-growing world of plastic manufacturing, we are continually on the lookout for innovative processes that allow us to deliver high-quality, custom plastic products to clients across a wide range of industries. One such manufacturing technique, vacuum forming, offers a unique combination of versatility and efficiency, making it a practical solution for producing large-scale components without sacrificing quality or precision. As a leading provider of plastic products in the Ottawa area, we pride ourselves on utilizing proven technologies like vacuum forming, helping us meet the diverse needs of our clients and exceed their expectations.
Vacuum forming, also known as thermoforming, is a plastic fabrication process in which a sheet of thermoplastic material is heated and then moulded onto a 3D form or mould using vacuum pressure. Once cooled, the formed plastic is removed from the mould, retaining its newly acquired shape. This process is popular for producing a variety of components, including COVID-19 countermeasures, marketing and display cases, podiums, election boxes, windshields, tables, and benches. Its cost-effectiveness and adaptability make vacuum forming an ideal choice for many large-scale projects requiring custom, intricately designed plastic components.
In this article, we will explore the science behind vacuum forming, delving into its numerous advantages and applications and how it compares to other plastic manufacturing techniques. Additionally, we will discuss crucial factors to consider when selecting vacuum forming for your project and provide insights into overcoming common challenges faced in the process. Join us as we uncover the immense potential of vacuum forming in plastic fabrication and learn how this efficient solution can contribute to the success of a diverse array of projects and industries.
Advantages of Vacuum Forming for Plastic Fabrication
Vacuum forming provides numerous advantages as a plastic fabrication method, particularly in large-scale production scenarios. These advantages include:
1. Cost-Efficiency: Vacuum forming requires less expensive tooling and moulds compared to other methods like injection moulding or CNC machining. This cost-effectiveness makes it an attractive option for large-scale projects and small businesses alike.
2. Design Flexibility: Vacuum forming can accommodate intricate and complex designs without the need for additional tooling or customized equipment, opening the door to endless possibilities when it comes to product customization.
3. Rapid Prototyping: The vacuum forming process allows for faster production of prototypes, making it easier to adapt designs and make improvements in the development phase.
4. Material Versatility: Vacuum forming is compatible with a wide range of thermoplastic materials, allowing the opportunity to select the ideal material based on the product’s required properties and specifications.
Applications of Vacuum Forming in Various Industries
The versatility of vacuum forming makes it a popular choice for various industries and applications, including:
1. COVID-19 Countermeasures: Vacuum forming has played a vital role in the quick production of plastic components like face shields and protective barriers, helping to protect frontline workers and the general public during the pandemic.
2. Marketing and Display Cases: With its flexibility and capacity for intricate designs, vacuum forming is the go-to method for creating eye-catching plastic display cases and marketing materials that draw attention and elevate branding efforts.
3. Automotive Industry: Vacuum-formed plastic components like windshields, interior panels, and light casings are common in the automotive sector, where large-scale production, design flexibility, and material versatility are essential.
4. Food Packaging: Vacuum forming is widely employed in the packaging industry, particularly for food products. The process can create protective, custom-fitted plastic containers that maintain shape integrity and preserve the freshness of the items within.
Factors to Consider When Selecting Vacuum Forming
To ensure the best possible outcomes when utilizing vacuum forming in plastic fabrication, consider the following factors when planning your project:
1. Material Selection: Choose a plastic material that is suitable for vacuum forming and fulfills the required properties of the specific project, such as strength, flexibility, or temperature resistance.
2. Mold Durability: Opt for high-quality moulds that can withstand multiple cycles of heating and cooling, ensuring consistent product quality throughout the production process.
3. Design Considerations: Carefully examine aspects of your product design, such as wall thickness, draft angles, and undercuts, to prevent complications or deformities during the vacuum forming process.
4. Production Volume: Vacuum forming is best suited for medium-to-high volume production, so carefully assess whether this method aligns with your project’s scale and timeline.
Overcoming Common Challenges in Vacuum Forming
Although vacuum forming offers numerous advantages, it is not without its challenges. Here are some common issues encountered in vacuum forming, along with advice on how to address them:
1. Webbing: Webbing occurs when the plastic material stretches unevenly, creating thin strands or “webs” of plastic in the final product. This issue can be mitigated by optimizing the mould design and ensuring uniform heating of the plastic sheet.
2. Material Sagging: Excessive sagging of the heated plastic material can lead to uneven thickness or deformities in the final product. Prevent sagging by using proper heating methods and optimizing the process parameters, such as temperature and heating time.
3. Air Trapping: Air may become trapped between the plastic sheet and the mould during vacuum forming, leading to defects in the final product. Address this issue by using properly designed vent holes or channels on the mould, which effectively evacuate air during the process.
Harnessing the Power of Vacuum Forming for Plastic Manufacturing Excellence
Vacuum forming is a powerful, versatile, and cost-effective solution for the large-scale production of custom plastic components. By understanding the fundamentals of this process, optimizing material selection and mould design, and addressing common challenges, you can efficiently utilize vacuum forming to create high-quality, functional parts tailored to your project’s unique needs.
Our team of plastic fabrication experts is committed to helping you achieve exceptional results with vacuum forming and other innovative manufacturing techniques. Reach out to us today, and let us guide you through the process of integrating plastic vacuum forming into your next project, ensuring unparalleled quality and efficiency for your diverse plastic manufacturing needs.