Top Uses of Vacuum Forming in Everyday Products
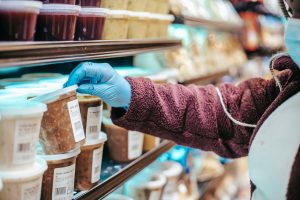
Vacuum forming is a fascinating process that shapes plastic into useful items we see and use every day. It involves heating a plastic sheet until it’s flexible, then stretching it over a mould while removing air to create a tight fit. This simple yet effective method is key in making many of the products we rely on.
From household items like food containers to parts in our cars, vacuum forming has a wide range of applications. It allows for creating items that are lightweight, durable, and cost-effective. This method is especially handy for making large or oddly shaped items that would be difficult or expensive to produce using other methods.
Understanding how vacuum forming works and its various applications can help us appreciate the technology behind the products we use. It’s amazing to think that a simple process like vacuum forming can create so many different things that make our lives easier and more convenient.
What is Vacuum Forming and How Does it Work?
Vacuum forming is a method used to shape plastic into specific forms. The process starts by heating a plastic sheet until it becomes soft and flexible. Once the plastic is ready, it is placed over a mould. The next step is to remove the air between the plastic and the mould. This is done using a vacuum, which sucks out the air, forcing the plastic to conform tightly to the shape of the mould. Once the plastic cools, it hardens into the shape of the mould, making a finished product.
The moulds can be made from various materials, such as wood, aluminium, or even clay, depending on what is being produced. The simplicity and efficiency of vacuum forming make it great for large or irregular-shaped items. Because the process is relatively cheap and fast, it’s a popular choice for both prototypes and mass production. This flexibility allows manufacturers to create many different kinds of products quickly and cost-effectively.
Household Items Made with Vacuum Forming
Vacuum forming is used to create many common household items that you might not even think about. The versatility of this method makes it perfect for a wide range of products found in homes. Here are some examples of household items made using vacuum forming:
1. Food Containers: Many of the plastic containers used to store food are made using vacuum forming. These containers are lightweight, durable, and can be made in various sizes and shapes.
2. Bathtubs and Shower Trays: Larger items like bathtubs and shower trays are often created using vacuum forming. The process allows for smooth surfaces and precise shapes, making these items both functional and aesthetic.
3. Light Fixtures: The plastic covers for ceiling lights and other fixtures are frequently made with vacuum forming. This method provides clear and durable light covers that are essential for home lighting.
4. Toys: Many plastic toys, especially larger ones like playhouses and slides, are made with vacuum forming. This ensures they are sturdy enough for children to play with and enjoy.
Knowing vacuum forming is behind so many household items makes it easier to appreciate the technology that helps make everyday life more convenient and comfortable.
Vacuum Forming in the Automotive Industry
Vacuum forming is widely used in the automotive industry to create various parts. This includes both interior and exterior components of vehicles. The process is perfect for making large and complex shapes, which are common in car design.
One of the most common uses of vacuum forming in cars is for dashboards. These need to be durable, heat-resistant, and precisely shaped to fit all the controls and displays. Vacuum forming ensures that dashboards meet all these requirements. Other interior parts, like door panels and seat backs, are also often made using this method.
For the exterior, vacuum forming is used to create parts like bumpers and fenders. These parts need to be strong yet lightweight, making plastic the ideal material. The precision of vacuum forming also means that these parts fit perfectly with the rest of the car, ensuring safety and proper aerodynamics. This versatility makes vacuum forming a crucial technology in the automotive industry.
Advantages of Using Vacuum Forming for Everyday Products
Vacuum forming offers several advantages that make it a popular choice for creating everyday products. These benefits help explain why this method is used so widely across different industries.
1. Cost-Effective: Vacuum forming is generally cheaper than other manufacturing methods. The moulds used in vacuum forming are relatively inexpensive to make, which helps keep the overall cost of production low.
2. Speed: The process is fast, allowing for quick production of large volumes. This is especially useful for items that need to be produced quickly to meet market demand.
3. Versatility: Vacuum forming can be used to create a wide range of products, from small, intricate parts to large panels. This versatility makes it suitable for many different applications.
4. Quality: The products made using vacuum forming are strong and durable. This ensures that they can withstand everyday use while maintaining their shape and functionality.
5. Customization: Vacuum forming allows for easy customization of products. This means that unique shapes and sizes can be created to meet specific needs.
Conclusion
Vacuum forming is an essential technology in creating many products we use every day. From household items to automotive parts, its versatility, cost-effectiveness, and speed make it a go-to method for manufacturers. Understanding how vacuum forming works and where it is used helps us appreciate the complexity behind the simple plastic items in our daily lives.
At Canus Plastics Inc., we specialize in creating high-quality products using advanced plastic vacuum forming techniques. Whether you need custom plastic solutions for your home or business, we’ve got you covered. Contact Canus Plastics Inc. today to see how we can help bring your projects to life with precision and reliability.