Vacuum Forming Basics and Uses
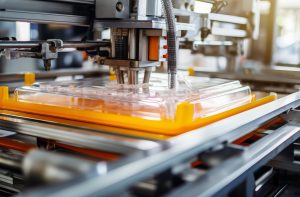
Vacuum forming is a neat way to shape plastic into all kinds of useful products. You have probably come across many vacuum-formed items without even realizing it. This process is simple yet incredibly versatile, making it a favourite in manufacturing.
The idea behind vacuum forming is straightforward. A plastic sheet is heated until it’s soft, then it is stretched over a mould. A vacuum sucks out the air, making the plastic conform tightly to the mould shape. After cooling down, the plastic becomes a strong and durable object with a specific form.
Understanding vacuum forming can open up a world of possibilities. From making food packaging and face shields to creating parts for cars and household items, vacuum forming plays a big role in many areas. This article aims to help you grasp the basics of vacuum forming, how it’s done, its pros and cons, and what it’s used for. Let’s dive in and explore the fascinating world of vacuum forming!
What is Vacuum Forming?
Vacuum forming is a method used to shape plastic materials. It involves heating a plastic sheet until it becomes soft and flexible. Once the plastic reaches the right temperature, it is placed over a mould. A vacuum then pulls the air out from between the plastic sheet and the mould. This makes the plastic tightly conform to the shape of the mould.
This process is popular because it’s simple and cost-effective. It allows for the creation of detailed and complex shapes with relatively low costs. Unlike other moulding methods, vacuum forming uses low-pressure techniques, which makes the process less expensive and easier to set up.
Different types of plastics can be used in vacuum forming. Common ones include polystyrene, polypropylene, and PVC. Each type of plastic has its own properties, making vacuum forming suitable for a wide range of applications. Polystyrene, for example, is often used for packaging because it is lightweight and easy to mould.
The Vacuum Forming Process Step-by-Step
The vacuum forming process involves several key steps. Here’s a simple breakdown of how it works:
- Heating the Plastic Sheet: First, a plastic sheet is placed into an oven and heated. The temperature needs to be just right to make the plastic soft and pliable without melting it. The sheet is usually clamped to hold it in place during this step.
- Positioning Over the Mould: Once the plastic sheet is heated, it is moved to the forming station. Here, the soft sheet is positioned over a mould. The mould can be made of wood, aluminium, or other materials, depending on the desired shape and details.
- Vacuum Application: After placing the plastic over the mould, a vacuum is applied. The vacuum removes the air between the sheet and the mould, causing the plastic to conform tightly to the mould’s shape. This step happens quickly, ensuring that the plastic takes on the precise form of the mould.
- Cooling and Finishing: Once the plastic has been shaped, it needs to cool down to retain its new form. Cooling can be done using air or water. After cooling, any excess plastic is trimmed away. Additional finishing touches can be added, such as drilling holes or smoothing edges.
This step-by-step process makes vacuum forming an efficient and effective way to create a variety of plastic products. It’s straightforward, yet it can produce highly detailed and high-quality items used in many industries.
Advantages and Disadvantages of Vacuum Forming
Vacuum forming has a lot of benefits, but it also has some drawbacks. Knowing these can help you decide if it’s the right process for your project.
Advantages:
- Cost-Effective: One of the biggest advantages is its cost. The equipment and moulds for vacuum forming are less expensive compared to other plastic forming methods. This makes it a good option for smaller budgets.
- Flexibility in Design: Vacuum forming allows for great flexibility in design. It can be used to make both simple and complex shapes. You can create detailed and precise forms, which is essential for custom or unique items.
- Fast Production: The process is relatively quick. Once the mould is ready, forming the plastic is a speedy process. This is helpful if you need to produce items in large numbers quickly.
Disadvantages:
- Material Limitations: Not all plastics are suitable for vacuum forming. Some materials might not heat evenly or could warp. This limits the types of plastics you can use.
- Detail Limitations: While vacuum forming can capture a lot of detail, it might not be as precise as other methods like injection moulding. Very fine details may not be as sharp.
- Waste Material: The process can produce excess material that needs to be trimmed away. This can result in some waste, which might not be ideal for all projects.
Understanding these pros and cons can help you choose the best plastic forming method for your needs.
Common Uses of Vacuum Forming
Vacuum forming is used in many fields for creating different products. Its versatility makes it a valuable process.
- Packaging: One of the most common uses is packaging. Vacuum forming helps create blister packs, clamshells, and other types of protective packaging. These are often seen in toy packaging, electronics, and food containers.
- Automotive Parts: The automotive industry uses vacuum forming to make various parts. Things like dashboards, door panels, and even small components can be produced this way. The parts need to be strong, lightweight, and fit perfectly.
- Medical Devices: Vacuum forming is perfect for creating items used in healthcare. This includes custom trays, protective covers, and components for medical devices. The process ensures these items are both sterile and durable.
- Retail Displays: Stores use vacuum-formed products to create eye-catching displays. This includes sign holders, display stands, and product organizers. These displays need to look good and be durable.
- Household Items: Everyday items like storage bins, trays, and even kitchen gadgets can be made using vacuum forming. The process allows for creating items that are both functional and affordable.
These examples show how vacuum forming is an essential part of making diverse and useful products for various sectors.
Conclusion
Vacuum forming is a valuable method for shaping plastic into all kinds of items. It’s easy to see why it’s so widely used when you consider its cost-effectiveness, speed, and flexibility. From packaging and automotive parts to medical devices and retail displays, vacuum forming plays a crucial role in multiple industries. It’s a straightforward process, yet it can produce high-quality, detailed, and durable products that we rely on every day.
If you’re interested in exploring vacuum forming for your project, Canus Plastics Inc. can help. Our expertise in plastic vacuum forming and other plastic shaping methods ensures we deliver top-notch results. Contact Canus Plastics Inc. to learn how we can assist you in creating high-quality plastic products that meet your needs. Let’s bring your ideas to life with precision and efficiency!