Thermoforming Essentials: How It Transforms Plastic Fabrication
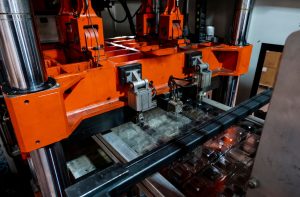
As a leading manufacturer and seller of quality plastic products in the Ottawa area, we pride ourselves on staying at the forefront of innovative fabrication technologies. One such technique that holds a pivotal position in our manufacturing process is thermoforming. Thermoforming has gained immense popularity across various industries, including COVID-19 countermeasures, safety and security, marketing and display cases, podiums, election boxes, windshields, tables, and benches, due to its efficiency, versatility, and cost-effectiveness.
Thermoforming is a plastic fabrication method that involves heating a thermoplastic sheet to a pliable state, followed by molding it to a desired shape using a rigid mold. The molded plastic sheet adheres to the contours of the mold as pressure or vacuum is applied. Once cooled and solidified, the finished part is trimmed, assembled, and further refined as per the requirements.
This informative blog post aims to provide a comprehensive understanding of the thermoforming process, its unique benefits, applications across different industries, and essential factors to consider when incorporating thermoforming into your fabrication projects. As a plastic fabrication expert, we believe in empowering our clients with the knowledge they need to make informed decisions, ensuring optimal outcomes for their products and businesses.
Benefits of Thermoforming in Plastic Fabrication
Thermoforming has garnered significant attention within the plastic fabrication industry, offering several compelling advantages compared to conventional manufacturing techniques:
- Cost-Effectiveness: Thermoforming requires less expensive tooling and equipment than other fabrication methods, such as injection molding. This translates to more budget-friendly production costs, particularly for small to medium-sized production runs.
- Time Efficiency: Thermoforming boasts quick turnaround times, thanks to relatively short heating and cooling cycles. This allows for speedy production and delivery of finished parts.
- Material Versatility: Thermoforming accommodates a diverse range of thermoplastic materials, including acrylic, polycarbonate, polyethylene, and more. This enables the creation of tailored products to suit specific client requirements.
- Design Flexibility: Thermoforming offers the ability to create complex and intricate shapes with ease, enabling the production of aesthetically pleasing and innovative designs.
- Environmentally Friendly: Thermoforming promotes waste reduction, as excess plastic materials can be re-melted and reused in subsequent manufacturing cycles.
Thermoforming Processes: Vacuum Forming and Pressure Forming
Two primary thermoforming methods dominate the industry: vacuum forming and pressure forming. These techniques involve distinct processes, each offering unique benefits depending on the project requirements.
- Vacuum Forming: Vacuum forming employs a vacuum to create negative air pressure beneath the heated plastic sheet, drawing it against the mold for precise shaping. Key advantages of vacuum forming include lower tooling and production costs, making it an ideal choice for projects with budget constraints or smaller production volumes.
- Pressure Forming: Pressure forming involves using positive air pressure to force the heated plastic sheet onto the mold. This method produces a higher level of detail and facilitates the creation of more complex shapes than vacuum forming. Consequently, pressure forming is suitable for projects requiring intricate designs or premium aesthetics.
Considerations for Thermoforming Success
When contemplating the use of thermoforming for a particular project, keep the following factors in mind for optimal results:
- Material Selection: Choose the appropriate thermoplastic material based on the project’s specific needs, such as strength, durability, UV-resistance, and aesthetics.
- Prototype Development: Invest time in developing accurate prototypes to ensure optimal fit, form, and function of the final product. This also aids in identifying potential issues early on, streamlining the production process.
- Mold Design: Thermoforming relies on precise and high-quality molds to achieve the desired product shape. Ensure that the mold design is appropriately engineered to accommodate the unique properties of the chosen thermoplastic material.
- Quality Assurance: Establish comprehensive quality control measures, including regular inspections, to verify that the final products meet the desired specifications and requirements.
Real-World Applications of Thermoformed Products
The cost-effectiveness, versatility, and design flexibility of thermoforming have made it indispensable in various industries. Here are a few real-world applications of thermoformed products:
- COVID-19 Countermeasures: Thermoformed plastic components are vital in the production of personal protective equipment (PPE), such as face shields, as well as sneeze guards and dividers for social distancing measures.
- Safety and Security: Thermoforming allows for the quick and efficient creation of security equipment, including protective enclosures, tamper-resistant locking mechanisms, and impact-resistant panels.
- Marketing and Display Cases: Thermoforming excels in crafting visually appealing custom display cases and signage that grab attention and promote brand visibility.
- Election Boxes and Podiums: Election boxes crafted using thermoforming techniques provide durability and security, while thermoformed podiums offer a sleek, professional appearance for any speaking engagement.
- Windshields and Protective Covers: Thermoformed windshields and protective covers provide enhanced durability and impact-resistance for vehicles, outdoor furniture, and recreational equipment.
Harness the Power of Thermoforming for Your Next Project
Thermoforming stands as a versatile, efficient, and cost-effective solution for creating a wide array of plastic products across various industries. By understanding the intricate details of the thermoforming process and recognizing the unique benefits of vacuum forming and pressure forming, you can make informed decisions that lead to superior outcomes for your products and overall business objectives.
Our experienced team is dedicated to guiding and supporting clients through each step of the thermoforming process, from material selection to quality control, ensuring the delivery of high-quality, tailored solutions that exceed expectations. Contact Canus Plastics Inc. today to explore how thermoforming can elevate your plastic fabrication projects to new heights.