The Remarkable Impact of CNC Machining in Plastic Manufacturing: Processes, Benefits, and Applications
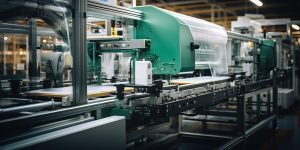
As a leader in manufacturing quality plastic products in the Ottawa area, we are dedicated to harnessing the power of innovative technologies, such as CNC machining, vacuum forming, thermoforming, general machining, polishing, welding, adhesives, and assembly, to create the perfect solutions for our clients. In this article, we’ll delve into CNC machining, a game-changing technology in plastics manufacturing, and explore its core processes, benefits, and wide-ranging applications across various industries.
CNC (Computer Numerical Control) machining revolutionizes plastic manufacturing by automating the fabrication process with high-precision machinery and advanced computer programming. This cutting-edge technology allows for increased precision, efficiency, and design-flexibility, fundamentally shaping plastic manufacturing in sectors such as COVID-19 countermeasures, safety and security, marketing and display cases, podiums, election boxes, windshields, tables, and benches.
The introduction of CNC machining into plastic manufacturing has shifted paradigms, enabling the creation of intricate and complex components with speed, accuracy, and cost-effectiveness that were previously unimaginable. By gaining a profound understanding of CNC machining processes, its advantages, and versatile applications, you’ll unlock the potential of this powerful technology to elevate your plastic manufacturing projects to new heights.
In this comprehensive guide, we’ll walk you through the exciting world of CNC machining, illustrating the transformative impact it has on plastics manufacturing. Furthermore, we’ll demonstrate how our team of experts at Canus Plastics Inc. can partner with you to harness CNC machining’s full potential to create bespoke, innovative solutions perfectly tailored to your project needs.
Understanding CNC Machining Processes
CNC machining is a broad term that encompasses several processes, each offering unique benefits and capabilities. By understanding the core processes involved in CNC machining, you can leverage this technology effectively for your plastic manufacturing projects:
1. Milling
CNC milling is a subtractive manufacturing process where material is strategically removed from a plastic workpiece using multi-axis rotary cutting tools. This versatile technique allows for the precise creation of various shapes, including flat surfaces, slots, pockets, and complex three-dimensional contours. CNC milling is commonly used in the production of automotive components, medical devices, and consumer electronics.
2. Turning
CNC turning involves the rotation of a workpiece while a cutting tool moves along its length, removing material to form cylindrical shapes. This process is ideal for producing parts with rotational symmetry, such as shafts, screws, and connectors. CNC turning ensures high accuracy and a smooth surface finish, making it a popular choice in various industries.3
3. Drilling
CNC drilling is a cutting process that utilizes multi-axis spindle movements to create precise holes in a workpiece. This process delivers high precision and repeatability, enabling the production of consistently accurate and uniform holes, essential for many plastic manufacturing applications.
4. Routing
CNC routing is a non-contact process where a high-speed rotating tool navigates across the workpiece’s surface, removing material to achieve the desired shape. This technique is particularly well-suited for cutting sheet materials, such as acrylics and polycarbonates, for use in signage, displays, and other large-format products.
Unlocking the Benefits of CNC Machining
CNC machining offers numerous advantages that make it an appealing choice for plastic manufacturing projects:
- Precision and Accuracy: CNC machining systems provide unmatched precision and accuracy, delivering consistently high-quality components with tight tolerances.
- Speed and Efficiency: CNC machines operate at a rapid pace and reduce production times by automating repetitive tasks that would otherwise take longer if performed manually.
- Enhanced Design Flexibility: CNC processes facilitate the creation of complex geometries that might be difficult or even impossible to produce using traditional manufacturing techniques.
- Material Versatility: CNC machining is compatible with a wide variety of plastics, including acrylics, polycarbonates, polytetrafluoroethylene (PTFE), and nylon, providing options for optimal material selection based on your project’s specific requirements.
Diverse Applications Across Industries
The unparalleled capabilities of CNC machining enable its use in various industries and applications, addressing challenges and solving problems on multiple levels:
- COVID-19 Countermeasures: CNC machining is instrumental in the production of critical components for COVID-19 protection equipment, test kits, and ventilators.
- Safety & Security: CNC processes enable the creation of highly precise, durable components in security equipment, surveillance cameras, and protective enclosures for electronic devices.
- Marketing & Display Cases: CNC machining techniques produce detailed and accurate components, resulting in visually appealing and structurally sound displays, signage, and custom-made product cases.
- Podiums, Election Boxes, and Furniture: CNC technology enables the creation of unique, sturdy, and aesthetically pleasing furniture items, including podiums, election boxes, tables, and benches.
Optimizing CNC Machining for Your Projects
Maximize the benefits of CNC machining for your plastic manufacturing projects by following these guidelines:
- Design for CNC Manufacturing: To achieve the best results, ensure that your component designs are optimized for CNC production, considering factors such as material properties, tool constraints, and cutting paths.
- Material Selection: Choose the appropriate plastic material for your project, considering factors like durability, rigidity, and chemical resistance, among others.
- Post-Processing: Evaluate the need for any post-processing steps, such as polishing or painting, and factor them into your production timeline and budget.
- Partner with a Trusted Supplier: Collaborate with a reliable CNC machining service provider with skilled professionals, technical expertise, and a track record of delivering high-quality solutions.
Final Thoughts: Transform Your Plastic Manufacturing with CNC Machining Expertise
Embracing CNC machining technology can elevate your plastic manufacturing projects, delivering exceptional precision, efficiency, and versatility. By understanding the core processes, benefits, and applications of CNC machining and partnering with a skilled and experienced provider, you can unlock the full potential of this transformative technology.
Our team at Canus Plastics Inc. is committed to providing top-notch CNC machining services and valuable insights to help bring your ideas to life. Get in touch with us today to discuss your CNC machining needs and discover how we can work together to create spectacular results for your plastic manufacturing projects.