The Power of Adhesive Bonding in Plastic Fabrication: Techniques, Advantages, and Applications
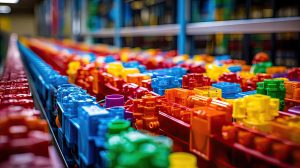
As a leader in manufacturing and selling quality plastic products in the Ottawa area, our expertise spans a diverse range of techniques, including CNC machining, vacuum forming, thermoforming, general machining, polishing, welding, adhesives, and assembly. In this article, we will focus on adhesive bonding, an important element of the plastic manufacturing process that offers invaluable advantages and functionality across numerous applications.
Exploring Different Adhesive Bonding Techniques
Adhesive bonding offers several techniques that complement various applications and materials. Understanding these different techniques is crucial in determining which method is the most suitable for your specific project requirements:
1. Solvent Bonding
Solvent bonding involves the use of solvents that partially dissolve the substrate materials, allowing them to fuse effectively when pressed together. This technique is particularly effective for bonding similar plastics, such as acrylics and polycarbonates. Solvent bonding is a popular choice in the plastic fabrication industry because it creates a smooth and nearly invisible bond, resulting in a clean and professional appearance.
2. Reactive Bonding
Reactive bonding involves the use of two-component adhesives that cure through a chemical reaction when mixed. Upon curing, these adhesives create strong and durable bonds between the substrate materials. Reactive adhesives are versatile and compatible with a wide range of plastics and other materials, making them suitable for numerous applications in diverse industries.
3. Hot Melt Bonding
Hot melt bonding utilizes thermoplastic adhesives that are applied in a molten state. These adhesives cool and solidify rapidly, creating a solid bond between the substrate materials. Hot melt bonding offers quick set times and can be easily reactivated with heat, providing flexibility for adjustments and modifications during the fabrication process.
4. Pressure-Sensitive Adhesive Bonding
Pressure-sensitive adhesive (PSA) bonding employs the use of adhesives that are inherently tacky and can adhere to surfaces upon contact with minimal pressure. PSAs offer flexibility in bonding different materials and are used for temporary as well as permanent applications, such as labels, tapes, and gaskets.
Uncovering the Advantages of Adhesive Bonding
Adhesive bonding presents numerous benefits that make it a preferred choice in plastic manufacturing processes:
1. Versatility
Adhesive bonding allows for the joining of different materials, including plastics, metals, glass, and composites. This versatility enables the creation of unique and innovative designs that may not be achievable using traditional fastening or welding methods.
2. Enhanced Aesthetics
Adhesives create seamless and nearly invisible bonds, contributing to a clean and professional appearance in the final products. This characteristic is particularly important for applications in marketing and display cases, where aesthetics play a crucial role in attracting and engaging an audience.
3. Flexibility and Stress Distribution
Adhesives offer flexibility and distribute stress evenly across the bonded area, reducing the risk of stress concentration and resulting material failures. This property is particularly beneficial in applications requiring resistance to the effects of thermal expansion, vibrations, and external forces.
4. Reduced Weight and Material Costs
Adhesive bonds eliminate the need for heavy mechanical fasteners and can simplify construction, often resulting in lighter assemblies and reduced material costs. This advantage is especially valuable in industries such as automotive and aerospace, where weight reduction is critical for fuel efficiency and performance.
Applying Adhesive Bonding Across Industries
The numerous advantages of adhesive bonding make it a go-to solution for various industries and applications:
- COVID-19 Countermeasures: Adhesive bonding plays a role in the assembly of personal protective equipment, health monitoring devices, and plastic barriers that help mitigate the spread of COVID-19 and safeguard public health.
- Safety & Security: The use of adhesive bonding in the assembly of security products, such as access control devices, surveillance camera housings, and protective covers, ensures a reliable and robust connection that withstands daily use and maintain their integrity in challenging environments.
- Marketing & Display Cases: Adhesive bonding is essential in creating visually appealing and structurally sound displays and signage by joining different materials seamlessly and contributing to the professional appearance of the final product.
- Furniture & Architectural Components: In the construction of tables, benches, podiums, and election boxes, adhesive bonding offers strength and durability while enhancing product aesthetics and reducing overall weight.
Maximizing Success with Adhesive Bonding
To fully harness the power of adhesive bonding for your plastic manufacturing projects, keep the following considerations in mind:
- Material Compatibility: Ensure that the selected adhesive is compatible with the substrate materials to achieve optimal bonding performance.
- Bonding Surface Preparation: Proper surface preparation, including cleaning and roughening, is essential to attain strong and durable adhesive bonds.
- Expertise and Experience: Partner with a knowledgeable plastic manufacturing provider that understands adhesive bonding techniques and can apply them effectively to your specific projects.
Unlock the Potential of Adhesive Bonding for Your Projects
Adhesive bonding represents a crucial element of the plastic manufacturing process, offering flexibility, reliability, and strength across numerous applications. By understanding the techniques, advantages, and applications of adhesive bonding, you can make informed decisions for your manufacturing projects and ensure successful outcomes.
At Canus Plastics Inc., we are committed to providing superior plastic products to meet a variety of needs. If you are looking for a plastics provider in Ottawa, get in touch with us today and discover how we can work together to create exceptional results for your plastic manufacturing projects.