Plastic Welding Techniques: Achieving High-Quality, Durable Joints in Plastic Manufacturing
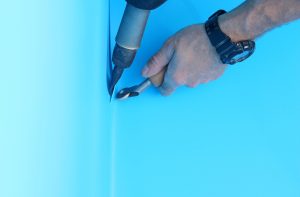
As experienced plastic manufacturers in the Ottawa area, we are passionate about delivering superior quality plastic products for various applications and industries. Our expertise spans CNC machining, vacuum forming, thermoforming, general machining, polishing, welding, adhesives, and assembly. In this article, we focus on plastic welding techniques and their significance in ensuring durable, long-lasting bonds in plastic manufacturing.
Plastic welding is the process of joining plastic pieces using heat, pressure, or a combination of both, depending on the technique employed. Plastic welding provides several advantages, including strength and durability, resistance to chemicals and water, and cost-effectiveness. This method of joining is highly sought after in numerous industries for various applications, such as safety and security, marketing and display cases, COVID-19 countermeasures, podiums, election boxes, windshields, tables, and benches.
By staying up-to-date with the latest advancements in plastic welding, we ensure our clients receive high-quality, reliable products to suit their needs. To better understand the role of plastic welding in manufacturing and its various techniques, join us in exploring the different methods, their advantages, and applications in the industry. If you’re searching for a partner for your next plastic manufacturing project, Canus Plastics Inc. is here to help you navigate the intricate world of plastic welding techniques and achieve exceptional results.
A Deep Dive into Plastic Welding Techniques
Several plastic welding techniques are in common use, each catering to specific material types, joint designs, and application requirements. In this section, we explore the most popular methods, highlighting their unique features and benefits:
1. Hot Gas Welding
Hot gas welding is a widely used technique for joining thermoplastics. It involves directing a stream of heated air or gas toward the plastic surface, softening it until it becomes malleable. A welding rod of the same material as the joined components is then introduced to bridge the gap, fusing the parts together. This technique is suitable for various materials, including polyethylene, polypropylene, PVC, and acrylic. Some of its advantages include cost-effectiveness, versatility, and a strong joint with minimal material degradation.
2. Ultrasonic Welding
Ultrasonic welding is an efficient, non-contact method for joining plastic materials. In this process, high-frequency vibrations generated by an ultrasonic device create heat and friction, causing the plastic materials to melt and bond together. Ultrasonic welding is especially useful for joining thin, semi-rigid plastics and is commonly used in the electronics, automotive, and food packaging industries. The main benefits of this technique include rapid cycle times, reduced energy consumption, and strong bond strength.
3. Friction Welding
Friction welding, as its name suggests, capitalizes on the heat generated by friction to bond plastic parts. In this method, one component is held stationary while the other is rotated. The two pieces come into contact, and the frictional heat melts the plastic surfaces, creating a bond. Friction welding is ideal for joining round, cylindrical, or irregularly shaped parts and is often employed in automotive and piping applications. This method offers advantages such as strong, leak-proof joints and lower energy consumption.
4. Spin Welding
Spin welding is a variation of friction welding specifically designed for plastics. One component is spun at high speeds against another stationary part in this process. The frictional heat generated melts the plastic surfaces, and the components are pressed together until a strong bond is formed. Spin welding is particularly suitable for joining circular components and boasts cost-effectiveness, faster production times, and strong, airtight joints.
Advantages of Plastic Welding in Manufacturing
Plastic welding techniques offer numerous benefits when it comes to manufacturing plastic products:
1. Strong and Durable Joints: Perhaps the most significant advantage of plastic welding is that it creates strong, durable joints capable of withstanding stresses, corrosive environments, and wear and tear.
2. Versatility: Various welding techniques cater to material types and part geometries. This versatility ensures that plastic welding can be applied in numerous industries and applications, from medical devices to automotive components.
3. Cost-Effectiveness: Plastic welding methods often require minimal equipment and lower energy consumption than other joining techniques. These factors contribute to overall cost savings through reduced production, maintenance, and material costs.
4. Environmentally Friendly: Most plastic welding techniques are considered eco-friendly, as they do not produce hazardous waste, minimize plastic waste, and require lower energy consumption.
Applications of Plastic Welding in Different Industries
Plastic welding plays an integral role in several industries thanks to its ability to create high-quality, resilient joints. Some typical applications include:
1. Medical Industry: In medical devices and equipment production, plastic welding techniques like ultrasonic welding create hermetically sealed joints that ensure sterility and non-contamination.
2. Automotive Industry: Friction and spin welding are used in the automotive sector to manufacture fuel tanks, light housings, and bumper components where strong, durable bonds are crucial.
3. Electronics Industry: Ultrasonic welding is the go-to method in electronics manufacturing to create reliable, watertight enclosures for sensitive electronic components.
4. Food Packaging: The food packaging industry uses plastic welding techniques like hot gas welding to provide secure, airtight seals that ensure product freshness and integrity.
The Importance of Choosing the Right Plastic Welding Technique
To achieve optimal results and ensure the longevity of the final product, selecting the appropriate welding technique is essential. Factors such as plastic material, part design, production requirements, and application specifications should be carefully considered when choosing the most suitable method. Engaging with an experienced plastic manufacturer who understands the intricacies of plastic welding can provide valuable guidance in making the best choice for your specific needs.
Trusting Expertise in Plastic Welding for Your Manufacturing Needs
By understanding the different plastic welding techniques available, their benefits, and their applications, you can make informed decisions when developing plastic products requiring robust, reliable joints. We are dedicated to offering our clients expert advice and services in the realm of plastic welding, ensuring that your projects achieve the highest standards of quality and durability. Reach out to Canus Plastics Inc. today to discuss your requirements and learn more about how our expertise in plastic welding can help bring your manufacturing projects to life.