How to Fix Warped Parts in Vacuum Forming
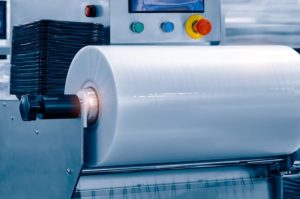
Vacuum forming is a popular plastic shaping method, but it can sometimes greet manufacturers with the issue of warped parts. Imagine crafting a plastic container, and just as it’s about to take shape, it appears misshaped and unbalanced. Warping can spoil the intended design and function of the product, making it important to understand and address it effectively. This is where understanding the mechanics of vacuum forming becomes crucial—not just for formulating a quick fix but for ensuring long-lasting quality.
The significance of tackling warping extends far beyond aesthetics. It’s about ensuring every item formed serves its purpose without compromise. Addressing warping correctly is an assurance of both quality and customer satisfaction. In many cases, professional services, like skilled welding, play an important role in resolving such deformities, particularly within Ottawa. The right approach can transform a warped product into a model of precision, providing a solid base for reliable manufacturing.
Understanding Warped Parts in Vacuum Forming
Warped parts in vacuum forming can be a real nuisance. Warping refers to the unwanted bending or twisting of the product, which often results from stresses introduced during the forming process. When you are relying on products to fit perfectly or look a certain way, a warped piece throws a wrench into the whole operation.
A few common causes lead to these issues, each requiring a specific approach to fix them effectively. One typical cause is uneven cooling. If parts of the material cool at different rates, it creates stress that makes the shape inconsistent. Material stress can also build up if the plastic sheet doesn’t respond well to temperature changes, often due to rapid heating or cooling. An ill-considered mould design might distribute pressure unevenly across the material, leading to an imperfect form.
Understanding these underlying issues is necessary for pinpointing the root cause of warping. For instance, if uneven cooling is the problem, focusing on the cooling process may solve it. If the mould design is at fault, it might need redesigning. By looking closely at these factors, anyone involved in vacuum forming can start addressing the root of the problem, paving the way for smooth, precise production.
Prevention Techniques
A stitch in time saves nine, and when it comes to preventing warping in vacuum forming, being prepared can save a lot of trouble. The process begins with selecting the right materials. The material has to withstand the heat and cooling process without stressing. Materials that expand predictably and cool uniformly tend to resist warping.
A smart mould design is also essential. A well-crafted mould distributes the material evenly, reducing the chance of uneven pressure that can lead to bumps and bends. It should support the plastic in such a way that shapes come out as intended every time. This calls for precision in every aspect of the mould’s build, with no unwanted cavities or sharp corners that might create localized stress points.
Temperature control is another pivotal factor. Maintaining a uniform temperature during the heating and cooling phases ensures that the material experiences even stress reduction. This counteracts the uneven shrinking or expansion that causes warping. Monitoring the temperature closely and making adjustments as needed provides the consistency required for flawless forms.
Taking these preventative measures offers the best shot at reducing warp risks effectively. By focusing on material choice, mould precision, and temperature regulation, vacuum forming can yield consistent, high-quality results.
Fixing Warped Parts
When a product does end up warped, don’t worry—there are ways to fix it. One approach involves reheating and reshaping the affected part. By applying consistent heat, you can soften the plastic enough to ease it back into its intended shape. This requires patience and a steady hand, as uneven heating might worsen the distortion. Think of reshaping as gently molding clay back into form, where precision and control are key.
For some parts, reinforcement techniques provide extra sturdiness during the reshaping process. This might involve adding support structures that maintain shape as the plastic cools. Supporting the structure as you work with it ensures that the shape remains stable once the material hardens again. This step might seem like a bit of an extra effort but can save a lot of time and material down the line.
Another effective solution is to seek out professional welding services, especially if you are in Ottawa. Qualified welders can offer specialized skills and tools that mend warped sections with precision. Welding involves the use of heat or pressure to fuse the warped parts correctly, providing a durable fix that blends seamlessly with the rest of the product. Having access to local experts can make a significant difference, turning a flawed item into a finished piece that looks and performs as expected.
Maintaining High-Quality Standards
Keeping up with regular maintenance on your equipment is an easy way to avoid many common issues in vacuum forming, including warping. Routine checks can uncover signs of wear and tear that might affect the forming process. Ensuring your machines are running smoothly will help maintain product integrity and reduce the risk of deformities.
Continuous monitoring of the forming process is also beneficial. Keeping a consistent eye on temperatures, material behaviour, and equipment performance can help identify problems before they fully develop. Think of it as a form of quality control that safeguards your production from unexpected hiccups. This proactive stance doesn’t just save time; it heightens the quality of your output.
Finally, investing in proper training for your team can yield big benefits in the long run. Well-trained workers are adept at identifying issues quickly and can adapt practices to meet the challenges of the task at hand. Their expertise enhances the entire production line, ensuring each step is carried out effectively. With skilled staff, you gain a significant advantage in avoiding complications while boosting overall efficiency.
Ensuring Long-Term Success
Understanding and addressing the challenges of warping in vacuum forming plays a pivotal role in the longevity of your manufacturing success. By consistently applying preventative techniques and fixing issues as they arise, your production line remains agile and effective. The result? A more reliable, streamlined process and products that meet both design and functional standards every time.
Staying updated with the latest practices in vacuum forming can also make a significant difference. As techniques evolve, keeping abreast of new methods and technologies can provide fresh insights into managing and reducing defects. Whether learning through industry networks, attending workshops, or engaging with peers, embracing continuous learning strengthens your capacity to adapt and thrive.
In summary, managing warping in vacuum forming isn’t just about addressing immediate problems but fostering a culture of quality and foresight. The strategies for prevention and repair, coupled with ongoing commitment to quality, laid here provide a pathway to crafting products that stand out in design and reliability.
Addressing warping issues effectively requires expert hands and tools. At Canus Plastics Inc., our experienced team is skilled in tackling such challenges, ensuring your products are precise and reliable. If you’re facing persistent warping problems, consider enlisting a welder in Ottawa to ensure flawless repairs and improvements. Let us support your production needs and transform your warped parts into perfect shapes, enhancing quality and customer satisfaction.