A Beginner’s Guide to Welding Plastic
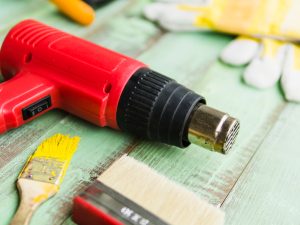
Plastic welding is a fascinating process that joins pieces of plastic together, much like metal welding. It transforms everyday items, making them sturdy and long-lasting. Whether fixing a plastic kayak or crafting intricate components for manufacturing, welding plastic lets you create strong bonds.
Different types of plastics need different welding methods. Knowing which plastics can be welded is crucial. Common materials suitable for welding include polyethylene and PVC, frequently seen in industrial and consumer products. These materials are found in various fields, from automotive to household goods.
Plastic welding offers many practical solutions in different industries. It’s used to make water tanks, fix car bumpers, and even create art pieces. Understanding how plastic welding works and what tools you need can open up a world of creativity and function. This guide will teach you the essentials, enhancing your skills in crafting and repairing durable plastic items.
Understanding Plastic Welding Basics
Plastic welding is a clever technique that joins two plastic pieces into one solid unit. It works by softening the surfaces of the plastic parts and then pressing them together to create a strong bond as they cool. This method is popular because it creates durable connections without needing extra fasteners or adhesives.
Various types of plastics are suitable for welding. Polyethylene (PE) and polyvinyl chloride (PVC) are the most common because of their thermoforming properties. Polypropylene (PP) and acrylics are also frequently used, each with specific applications and benefits that match different project needs. Choosing the right plastic is essential for successful welding, as mixing incompatible plastics can lead to weak joints.
Plastic welding finds applications in many industries. It’s used in automotive repair for bumpers and fuel tanks, in the medical field for items like components for devices and instruments, and in construction for assembling pipelines and other infrastructure. Artistic fields use it for making sculptures and displaying installations, showing its versatility across different areas.
Essential Tools and Materials for Plastic Welding
Creating strong welds requires specific tools and materials. Having the right equipment makes the process smoother and the results more reliable. Here are the basics needed for plastic welding:
- Welding Rods: These are strips of plastic that melt along with the parts being joined, acting as a filler to strengthen the weld. It’s important to choose rods made from the same type of plastic as the pieces being welded.
- Heat Guns: These tools blow hot air onto the plastic to soften it. Adjustable temperature and nozzle settings help match the process to different types of plastic.
- Welding Tips: Attachments for heat guns that focus heat in a specific area, ensuring precise application and control over the welding process.
- Safety Gear: Always wear safety glasses to protect from flying debris and gloves to guard against burns. A respirator can be necessary in enclosed spaces to avoid inhaling fumes.
To ensure safety, proper gear is essential. Items like a fire extinguisher and a well-ventilated workspace are also beneficial. Choosing the right equipment and precautions enhances both safety and effectiveness, paving the way for successful plastic welding projects.
Step-by-Step Plastic Welding Techniques
Welding plastic can be a rewarding skill, allowing you to repair or create products with a durable finish. Start by preparing the surfaces. Clean them thoroughly to remove grease, dust, or any debris that might prevent a proper bond. Slightly roughen surfaces with sandpaper to enhance adhesion.
There are several methods to weld plastic. The most common is hot air welding, where a heat gun softens the plastic. This process requires you to move the tool evenly along the joint while applying a plastic welding rod for a seamless bond. Ultrasonic welding uses high-frequency sound waves to melt and join plastics without the need for rods, often used in assembly lines for smaller items. Extrusion welding involves a hand-held extruder that feeds out a bead of molten plastic to join larger or thicker materials.
To achieve strong and durable welds, keep a steady hand and consistent speed when welding. Practice on scrap materials until you are comfortable with the tools and methods. Control the temperature closely; too hot, and the plastic can burn or degrade, too cold, it won’t bond properly.
Troubleshooting Common Welding Issues
Even with practice, welding isn’t without its challenges. One common issue is weak weld lines, often caused by incorrect temperature settings or insufficient cleaning. Make sure to adjust the temperature according to the specific plastic type and always prepare surfaces properly.
Another frequent problem is bubbling or distortion, usually arising from overheating. Reduce the heat or increase airflow if you notice these symptoms. Misalignment can lead to poor seam strength. To avoid this, use guides or clamps to hold pieces securely in place during welding.
Maintenance of your equipment is crucial to prevent defects. Keep your welding tools clean and regularly check for wear and tear, especially on heat elements and nozzles. Replace parts as needed to maintain performance and safety.
Ensure you follow these practices to enhance the quality of your welds. Careful attention to these details helps to create neat, strong, and reliable plastic joins.
Conclusion
Mastering plastic welding opens up wide possibilities in crafting and product creation. With the right techniques, you can repair, construct, or customize items to suit many practical needs—from simple home repairs to complex industrial applications. This skill supports the creation of sturdy and aesthetically pleasing products designed to withstand daily rigours and challenges.
Understanding the different welding methods and troubleshooting issues enhances your ability to create reliable bonds and transform ordinary materials into exceptional products. Continued practice and learning help refine these skills, unlocking more advanced applications and innovative solutions.
Whether you’re new to plastic welding or looking to upgrade your skills, Canus Plastics Inc. is ready to support your journey. Our welders in Ottawa offer you the tools and knowledge needed to excel in all your welding projects. Explore our wide range of plastic solutions and discover how Canus Plastics Inc. can partner with you in creating more robust, high-quality products.