Exploring Thermoforming Technologies: Understanding Key Processes and Their Applications in Plastic Manufacturing
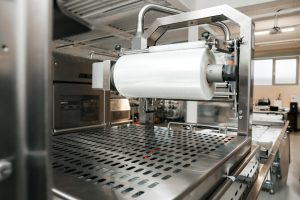
As a leader in manufacturing quality plastic products in the Ottawa area, we utilize an array of innovative technologies, including CNC machining, vacuum forming, thermoforming, general machining, polishing, welding, adhesives, and assembly, to deliver optimal results for our clients. In this insightful article, we’ll discuss thermoforming—one of the vital techniques in the world of plastic manufacturing—and examine its key processes, benefits, and diverse applications across various industries.
Thermoforming is a plastic manufacturing process that involves heating a plastic sheet until it becomes malleable, followed by molding it into the desired shape using a mold (either male or female) and applying pressure. Once the plastic cools and hardens, it retains the shape of the mold, resulting in a lightweight and durable component. Thermoforming is a popular choice for creating plastic products for a wide range of applications, including COVID-19 countermeasures, safety and security, marketing and display cases, podiums, election boxes, windshields, tables, and benches. The technique stands out due to its capability to offer quick processing, cost-effectiveness, and flexibility in design and production.
By understanding the fundamentals of thermoforming technology, its processes, and its applications in various industries, you’ll gain valuable insights that will help you make informed decisions when designing and fabricating plastic products. In this article, we’ll guide you through the fascinating realm of thermoforming, unveiling the inner workings of this technique and how our team of experts at Canus Plastics can help you unlock its potential to power your product development projects to success.
Crucial Thermoforming Processes
Thermoforming encompasses a wide range of processes, each offering distinct advantages depending on the specific project requirements. To make the most of thermoforming technology, it’s vital to understand the key processes and their ideal utilization:
1. Vacuum Forming
Vacuum forming, a subset of thermoforming, involves heating a plastic sheet and placing it over a mold before using vacuum pressure to draw the material into the mold’s shape. This process is ideal for creating relatively simple and shallow shapes, such as trays, display cases, and vehicle components.
2. Pressure Forming
Pressure forming works similarly to vacuum forming but uses positive air pressure in addition to vacuum pressure, thus allowing for more intricate shapes, defined edges, and enhanced detailing. Pressure forming is ideal for applications requiring precise, aesthetically pleasing components, such as medical equipment enclosures and consumer product packaging.
3. Drape Forming
Drape forming is a variant of thermoforming used for bending plastic sheets to create curved components. A heated plastic sheet is draped over a mold, taking on the desired curvature as it cools. Drape forming is commonly employed in the production of windshields, displays, and lighting components.
4. Twin-sheet Forming
Twin-sheet forming involves the simultaneous heating and molding of two separate plastic sheets that are then fused together, creating a hollow, rigid structure. This technique is ideal for projects requiring enclosed, lightweight components, such as air ducts, fuel tanks, and storage containers.
Advantages of Thermoforming
Thermoforming offers numerous benefits that make it an attractive choice for a wide range of plastic manufacturing applications:
- Cost-effectiveness: Thermoforming provides lower tooling and production costs compared to other plastic manufacturing techniques, such as injection molding, making it more affordable for small to mid-sized production runs.
- Rapid Prototyping: Thermoforming technology enables quick creation of prototypes, allowing you to test and refine your product designs before moving to full-scale production.
- Design Flexibility: Thermoforming facilitates the manufacturing of diverse shapes and sizes, granting you greater freedom in product design and customization.
- Material Versatility: Thermoforming is compatible with various types of thermoplastics, such as ABS, polycarbonate, PET, and more, allowing you to choose the best material for your specific project.
Applications in Diverse Industries
Thermoforming techniques are employed in a broad array of industries, creating versatile and durable products tailored to meet specific demands:
- COVID-19 Countermeasures: Thermoforming is crucial in manufacturing protective equipment, such as face shields and barriers, helping reduce the spread of COVID-19.
- Safety & Security: From safety screens to protective covers, thermoforming techniques contribute to the production of reliable safety and security equipment.
- Marketing & Display Cases: Thermoformed components create visually stunning, sturdy display cases and other marketing materials for showcasing products in an engaging manner.
- Podiums, Election Boxes, and Furniture: Thermoforming is instrumental in manufacturing durable, functional, and aesthetically pleasing products, such as podiums, election boxes, and other furniture items.
How to Optimize Thermoforming for Your Projects
Maximize the potential of thermoforming technology for your plastic manufacturing projects by following these guidelines:
- Select the Right Material: Make an informed decision when choosing thermoplastics for your project, considering factors like strength, transparency, and rigidity.
- Design Optimization: Collaborate with design and engineering teams to develop an optimized product design that addresses functional, aesthetic, and cost considerations.
- Mold Material and Quality: Choose the appropriate mold material (such as aluminum or composite) and ensure proper mold maintenance to guarantee the longevity and quality of your thermoformed products.
- Partner with a Skilled Manufacturer: Work with an experienced thermoforming manufacturer who understands the intricacies of the process and can provide expert guidance throughout your project.
Revolutionize Your Product Development with Thermoforming Expertise
Thermoforming technologies offer incredible potential for driving innovation, efficiency, and success in your plastic manufacturing endeavors. By understanding the key processes, benefits, and applications of thermoforming—and leveraging the expertise of a skilled partner—you can transform your product development process and achieve outstanding results.
Our team at Canus Plastics is committed to providing exceptional service, valuable insights, and innovative thermoforming solutions to bring your ideas to life. Contact us today to discuss your needs for plastic for thermoforming and discover how we can help you revolutionize your product development endeavors.