The Art of Plastic Welding: Techniques, Applications, and Benefits in Custom Plastic Product Manufacturing
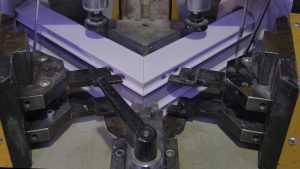
As a leading manufacturer and seller of quality plastic products in the Ottawa area, we take pride in our proficiency in various cutting-edge technologies and techniques that help us create innovative, durable, and functional products. Among these techniques, plastic welding is an indispensable method that plays a crucial role in assembling custom plastic products, serving diverse industries and applications such as COVID-19 countermeasures, safety and security, marketing and display cases, podiums, election boxes, windshields, tables, and benches.
Plastic welding involves joining or fusing two or more plastic components by applying heat and pressure to create a strong bond. It is a fundamental process in assembling custom plastic products, ensuring secure connections and durable construction. Utilizing various plastic welding methods, including hot gas welding, ultrasonic welding, and laser welding, requires expertise and precision to achieve optimal results that meet industry standards.
In this insightful blog, we will delve deep into the fascinating world of plastic welding, exploring different welding techniques, their applications in various industries, and the myriad advantages they bring to plastic product manufacturing. Furthermore, we will discuss the factors to consider when choosing the right plastic welding method for your project, ensuring you achieve the strongest, most durable bonds.
Exploring Various Plastic Welding Techniques
There are several plastic welding techniques, each with its unique characteristics, advantages, and applications:
- Hot Gas Welding: This technique uses a heat gun to direct hot air between plastic components that have been slightly softened, allowing them to bond. Hot gas welding is suitable for materials like Polyethylene (PE), Polypropylene (PP), and PVC.
- Ultrasonic Welding: Ultrasonic welding uses high-frequency sound waves to create friction and vibration, generating heat to bond plastic components. It’s an efficient method for joining thin, rigid materials and is commonly used in the electronics, automotive, and packaging industries.
- Laser Welding: In laser welding, a laser beam is employed to deliver a highly focused and intense heat source, melting the plastic components and creating a strong bond. Laser welding is suitable for intricate, small-scale components, often used in medical devices and electronics manufacturing.
- Vibration Welding: This process uses vibrations to generate heat and fuse plastic components. The vibrating motion creates friction, ultimately melting and joining the materials. Vibration welding works well for larger, more complex components, such as automotive parts.
Various Applications of Plastic Welding Across Industries
Plastic welding is widely employed in various industries due to its versatile nature:
- COVID-19 Countermeasures: Plastic welding helps assemble protective barriers, shields, and partitions, contributing to safer environments during the pandemic.
- Safety and Security: Plastic welding is crucial in manufacturing security enclosures, road barriers, and protective bollards for enhanced public safety.
- Marketing and Display Cases: Robust, visually appealing plastic display cases and signage rely on plastic welding for sturdy construction and professional appearance.
- Podiums and Election Boxes: Durable podiums and transparent election boxes, made from precisely welded plastic components, ensure long-lasting use and integrity.
- Windshields and Protective Covers: Welded plastic components form strong, resilient windshields and covers, offering protection against the elements and extending the product’s lifespan.
The Advantages of Plastic Welding in Custom Product Manufacturing
Plastic welding offers numerous benefits in the realm of custom plastic product manufacturing:
- Strength and Durability: Properly welded plastic joints provide strong, long-lasting bonds that can withstand rugged use and environmental stresses.
- Versatility: Plastic welding can be applied to various materials and component sizes, supporting diverse applications and industries.
- Speed and Efficiency: Some plastic welding methods, such as ultrasonic or laser welding, are rapid and efficient, reducing production time and cost.
- Aesthetics: Plastic welding creates clean, visually pleasing joints, contributing to a professional, high-quality appearance for your finished products.
Factors to Consider When Choosing a Plastic Welding Technique
Choosing the right plastic welding technique is crucial for the success of your custom plastic manufacturing project. Consider the following factors:
- Material Compatibility: The type of plastic material used in your project determines the appropriate welding technique. Ensure that your chosen method is compatible with the materials you are using.
- Component Size and Complexity: Some welding techniques, such as vibration welding, are better suited for larger, more complex components, while methods like laser welding thrive on intricate, small-scale work.
- Production Volume and Speed: The welding method should align with your desired production speed and volume. For instance, ultrasonic welding is a fast process that could benefit projects requiring rapid production.
- Finish and Aesthetics: The chosen welding technique should produce visually pleasing, smooth joints that enhance your product’s overall appearance and appeal.
Harness the Power of Plastic Welding for Custom Plastic Product Manufacturing
Understanding the art of plastic welding, its various techniques, applications, and benefits can dramatically impact the quality and durability of your custom plastic products. You can make informed decisions and achieve exceptional results by analyzing factors such as material compatibility, component size, and production speed.
Canus Plastics Inc.’s team of experienced professionals is prepared to guide you through the entire plastic welding journey, sharing best practices and offering advice that ensures the success of your plastic manufacturing projects. Reach out to us today to discover how our plastic welding expertise can elevate your custom plastic products to new heights of excellence.