Effective Welding Techniques in Plastic Fabrication
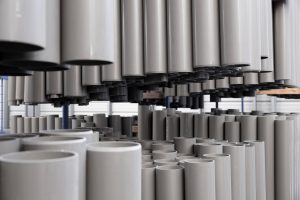
Welding is a crucial technique in plastic fabrication that helps us join separate plastic pieces into one strong and cohesive unit. This process involves melting the surfaces of the plastics to be joined and allowing them to fuse as they cool.
Effective welding ensures a strong bond that can withstand various stresses and environmental factors. By using advanced welding techniques, we can create durable and reliable plastic products.
Understanding Plastic Welding: An Overview
Plastic welding is a technique used to join pieces of plastic together by heating the surfaces to the point where they melt and then applying pressure to fuse them. This process creates a strong, seamless bond that is essential for many plastic products. Welding is particularly crucial in creating items that need to be waterproof, airtight, or capable of withstanding significant stress.
We use various types of plastic materials, each requiring specific welding methods to ensure the best results. For instance, the type of plastic, its thickness, and the intended use of the final product all influence the welding technique chosen. Welding in plastic fabrication is different from welding metals, as it requires lower temperatures and specialized equipment to avoid damaging the material.
Popular Welding Techniques for Plastic Fabrication
1. Hot Gas Welding: This technique involves using a jet of hot air to heat the plastic surfaces that need to be joined. A filler rod made of the same material is also heated and used to fill the joint. This method is ideal for repairing damaged plastic parts and is often used for items that have intricate shapes or are hard to reach.
2. Ultrasonic Welding: This method uses high-frequency ultrasonic vibrations to create heat at the joint area. The vibrations cause the plastic molecules to move rapidly and generate heat, which melts the material and creates a bond. Ultrasonic welding is precise and efficient, making it suitable for small parts and detailed work.
3. Spin Welding: In this technique, one of the plastic parts is rotated at high speed while in contact with the other part. The friction generates heat, which melts the surfaces of the plastics and bonds them together when the rotation stops. Spin welding is used for round or cylindrical parts, such as pipes and containers.
4. Laser Welding: Laser welding involves using a focused laser beam to heat the plastic along the joint line. This method offers high precision and control, making it ideal for delicate or complex parts. Laser welding is commonly used in the production of electronic components and medical devices.
Applications of Effective Plastic Welding
Effective plastic welding is essential in many different fields due to its ability to create strong and durable bonds. One significant application is in the production of COVID-19 countermeasures. For example, welded plastic face shields and barriers provide vital protection and must be reliable and sturdy. Effective welding ensures that these items can endure regular use and cleaning without falling apart.
Another critical area is safety and security products. Welding is used to create sturdy enclosures, protective coverings, and safety barriers. These products often need to meet strict safety standards, and effective welding is key to their strength and reliability. Marketing and display cases also benefit from plastic welding. The seamless bonds created through welding contribute to a clean, professional look that showcases products attractively and securely.
Other applications include the manufacturing of podiums, election boxes, windshields, tables, and benches. These items require strong structural integrity to ensure long-lasting use. By employing effective welding techniques, we can produce items that meet high durability standards and perform well under various conditions.
Ensuring Quality and Precision in Plastic Welding
To ensure high quality and precision in plastic welding, we start by selecting the right materials. Using suitable plastics that melt and bond well together is essential. This step helps in achieving strong and durable joints. We also use advanced welding equipment that allows us to control heat and pressure accurately. This technology helps in creating consistent and precise welds.
Regular inspections and quality checks are crucial in maintaining high standards. Each product undergoes thorough testing to ensure that the welds are strong and meet the required specifications. Making adjustments and improvements based on these tests helps us refine our techniques and produce better-quality products.
We also focus on continuous training for our staff. Skilled and knowledgeable workers are better equipped to handle the complexities of plastic welding. Ongoing training ensures that our team stays updated with the latest methods and technologies, allowing us to maintain a high level of craftsmanship.
Conclusion
Plastic welding plays a critical role in the fabrication of many essential products. From safety equipment to display cases and beyond, effective welding techniques ensure that our products are strong, durable, and meet precise specifications. By choosing the right materials, utilizing advanced technology, conducting rigorous quality checks, and training our staff, we can maintain high standards in our welding processes.
Understanding and applying the best welding techniques allows us to create plastic products that perform well and last longer. For those seeking top-quality plastic fabrication, reaching out to Canus Plastics Inc. will connect you with experts dedicated to excellence in plastic welding. Let us help you achieve the perfect solution for your needs!