The Basics of Vacuum Forming: What It Is and How We Use It
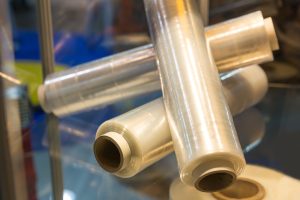
At Canus Plastics Inc., we specialize in transforming durable plastic sheets into a variety of intricate designs through a process known as vacuum forming. This technique, central to our production operations, allows us to efficiently create components that are integral to a wide range of our products, from COVID-19 countermeasures to sophisticated marketing displays. Vacuum forming is not just about shaping plastic; it is about mastering precision to deliver tailor-made solutions that meet the unique needs of each client.
Vacated air is the secret behind vacuum forming. By heating plastic sheets until they’re pliable, and then drawing them over a mold using a high-powered vacuum, we can achieve detailed shapes with meticulous accuracy. This method not only ensures repeatability for mass production but also allows for the customization of designs with ease. The flexibility and efficiency of vacuum forming make it a preferred choice not only in the plastic industry but also across various sectors requiring high-quality, durable plastic products.
As leaders in the industry, we harness the inherent advantages of vacuum forming to offer our clients products that combine functionality with aesthetics. Whether creating sleek windshields, robust safety barriers, or elegant display cases, our vacuum-formed products stand out for their quality and durability. Let’s delve deeper into how this technology shapes the backbone of our operations and the myriad products we craft.
Understanding Vacuum Forming: An Overview
Vacuum forming is a simplified molding process that transforms plastics into various useful products by heating sheets of plastic and drawing them into a mold using a vacuum. At Canus Plastics Inc., we utilize this technique to convert flat plastic sheets into intricate shapes that meet specific customer requirements. This process not only supports the versatility of product design but also enhances the utility and aesthetics of the final product.
The origins of vacuum forming trace back to the 1930s, shortly after the development of the first vacuum cleaner. Over the years, it has evolved significantly and has been adopted widely across different industries due to its efficiency and cost-effectiveness. The basic vacuum forming process involves heating a plastic sheet until it becomes flexible, then stretching it over a mold and applying a vacuum to shape the plastic to the mold’s contours before it cools and hardens. This straightforward yet dynamic process allows for quick production cycles and detailed precision in large-scale product manufacturing.
The Role of Vacuum Forming in Our Product Line-up
Vacuum forming plays a critical role in our diverse range of products. For instance, we create components for COVID-19 countermeasures and protective barriers, which require sturdy and reliable plastics. Our marketing and display cases, crafted through vacuum forming, not only protect valuable items but also showcase them attractively, making them perfect for retail environments. Additionally, our election boxes are manufactured using this technology to ensure security and durability.
The advantages of using vacuum forming in manufacturing these products are significant. Firstly, the method allows for the production of lightweight yet robust parts, which is essential for both portability and durability. Secondly, vacuum forming provides us with the flexibility to produce complex shapes that would otherwise be difficult or too costly with other techniques. Lastly, vacuum forming is highly adaptable to customer-specific requirements, making it ideal for custom orders that require unique shapes and sizes.
By integrating vacuum forming into our production line, Canus Plastics Inc. has not only enhanced the quality and functionality of our products but also ensured that we can meet diverse market needs effectively and efficiently. This method’s ability to handle various plastics and its low-cost tooling compared to other forming techniques like injection molding, allows us to keep our products affordable without compromising on quality or design precision.
Detailed Steps in the Vacuum Forming Process
At Canus Plastics Inc., every detail in the vacuum forming process is carefully managed to ensure optimal quality and precision. The first step involves preparing the plastic sheet. We select a suitable plastic material based on the product specifications—commonly used plastics include acrylic, PETG, and polystyrene. The chosen sheet is then carefully cut to size to fit the forming machine and aligned properly to ensure an even forming process.
The next stage is heating and molding. The plastic sheet is placed in the vacuum forming machine where it’s heated until it becomes soft and pliable. Once the right temperature is reached, the soft plastic is then draped over a mold. We then apply a strong vacuum that sucks the air out between the plastic sheet and the mold, causing the plastic to conform tightly to every contour of the mold. This process is crucial as it defines the intricacies and precision of the product’s design.
After the molding, the formed plastic needs to cool and solidify into its new shape. We ensure controlled cooling to prevent warping or distortion. Once the plastic has cooled and hardened, it is released from the mold. The final products are then trimmed of any excess material, inspected for quality, and finished with any additional detailing required.
Why Choose Vacuum Formed Products for Specific Needs
Choosing vacuum-formed products offers significant advantages, particularly in terms of cost-effectiveness, versatility, and durability. Vacuum forming allows us to produce large or complex shapes at a lower cost compared to other manufacturing methods. This cost advantage is passed on to our customers, making vacuum-formed products an economical choice for both small and large batches.
The versatility in shapes and sizes that vacuum forming offers is unparalleled. With our advanced technology, we can create detailed molds that meet any design requirement, from intricate marketing display cases to large, smooth windshields. This flexibility makes vacuum-forming an ideal choice for a wide range of applications across various industries.
Moreover, the durability of vacuum-formed pieces ensures long-lasting products that maintain their aesthetics and functionality over time. The materials we choose and our precise forming process contribute to the strength and resilience of the finished products, making them suitable for both indoor and outdoor use in demanding conditions.
Final Thoughts
As we continue to innovate and refine our vacuum forming processes at Canus Plastics Inc., we remain committed to delivering high-quality, cost-effective, and reliable solutions to meet the diverse needs of our clients.
Visit Canus Plastics Inc. to explore how our vacuum forming solutions can enhance your product offerings. Dive into our versatile range of plastic products, crafted to perfection, and see how they can contribute to your success. Inviting you to collaborate with us; let’s shape your ideas into reality with precision and innovation.