Vacuum Forming: Uncovering its Advantages and Applications in Custom Plastic Product Manufacturing
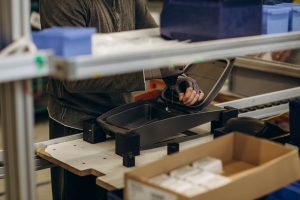
As a frontrunner in manufacturing and selling quality plastic products in the Ottawa area, we are dedicated to unlocking the full potential of innovative technologies and processes. One essential technique that continues to transform custom plastic product manufacturing is vacuum forming. This versatile and cost-effective method is ideally suited for creating a wide range of products, including COVID-19 countermeasures, safety and security equipment, marketing and display cases, podiums, election boxes, windshields, tables, and benches.
Vacuum forming is a type of thermoforming, where a plastic sheet is heated until soft and then positioned over a mold or form. A vacuum is applied, drawing the sheet tightly around the mold, resulting in precise and uniform shaping. After cooling, the plastic retains its new shape and can be removed from the mold, trimmed, and finished. This process allows for the efficient creation of large or intricate plastic components with intricate detailing.
In this insightful blog, we will delve into the mechanics of vacuum forming, highlighting its advantages, applications, and best practices to produce outstanding custom plastic products aligned with your vision. Furthermore, we will share essential factors to consider when deciding if vacuum forming is the ideal choice for your project, helping you make informed decisions and optimize your manufacturing process.
Exploring the Benefits of Vacuum Forming
Vacuum forming offers several compelling advantages over alternative plastic manufacturing techniques, including:
- Cost-Effectiveness: Vacuum forming requires less expensive tooling than traditional methods, making it an ideal option for small-batch projects or streamlined production processes.
- Production Speed: Vacuum forming allows for rapid development and manufacturing of custom plastic components, as reduced tooling requirements and efficient use of materials result in shorter lead times.
- Design Flexibility: This versatile process enables the creation of intricate and complex geometries, including undercuts, embossing, and deep draws. This flexibility enhances design capabilities and broadens the scope of potential applications.
- Material Versatility: Vacuum forming supports a wide range of plastic materials, providing ample choices to fulfill specific project requirements and customer preferences.
Real-World Applications of Vacuum Forming
Vacuum forming’s versatility imbues it with the ability to serve a variety of applications across diverse industries:
- COVID-19 Countermeasures: Vacuum-formed plastic shields, barriers, and sanitization stations provide vital protection during the ongoing pandemic.
- Safety and Security: Custom protective enclosures, guards, and other safety equipment benefit from the precision and durability of vacuum-formed plastic components.
- Marketing and Display Cases: Vacuum forming is an ideal choice for crafting eye-catching and robust display cases, signs, and other marketing materials.
- Podiums and Election Boxes: The use of vacuum forming imparts a high-quality finish and robust construction on these highly visible, professional items.
- Windshields and Protective Covers: Tailored windshields and covers can be created with exceptional precision owing to vacuum forming’s advanced capabilities.
Best Practices for Successful Vacuum Forming Projects
To ensure vacuum forming success, adhere to these best practices:
- Material Selection: Choose the appropriate plastic material suited to the specific product’s performance requirements, such as strength, durability, or flexibility.
- Mold Design: Develop a mold with vacuum-forming compatibility, taking into account factors such as draft angles, surface finish, and necessary venting.
- Process Optimization: Use the right combination of heating temperatures, molding pressures, and cooling times to optimize the vacuum forming process and achieve optimal product quality.
- Trimming and Finishing: Utilize precise guidelines and techniques during the trimming and finishing stages to ensure the end product adheres to the highest quality standards.
Factors to Consider When Choosing Vacuum Forming for Your Project
Before selecting vacuum forming as the ideal process for your project, consider these critical factors:
- Part Size and Complexity: Vacuum forming is best suited for larger components with moderate to high levels of intricacy. Assess if your project aligns with these requirements before committing to this process.
- Production Volume: Vacuum forming is a cost-effective choice for smaller production runs due to lower tooling costs. However, for higher-volume projects, other techniques may offer more competitive pricing.
- Material Thickness: Vacuum forming is generally limited to thinner materials, as thicker plastics may pose challenges during the molding process. Ensure the material thickness is compatible with the intended application.
- Tolerances and Precision: While vacuum forming is capable of producing components with good dimensional accuracy, other processes may achieve tighter tolerances if required.
Harnessing the Power of Vacuum Forming for Incredible Custom Plastic Products
Navigating the realm of vacuum forming equips you with invaluable knowledge and insights, enabling you to make informed decisions and deliver outstanding custom plastic products. By weighing various factors and adhering to best practices, you can harness vacuum forming’s full potential to fulfill diverse industry needs and create eye-catching, robust plastic components.
Our dedicated team of experts is ready to share their wealth of experience, supporting you throughout the entire plastic vacuum forming process, from design to production. Reach out to Canus Plastics Inc. today to explore the possibilities of vacuum forming and elevate your custom plastic product manufacturing to the next level.