Choosing the Right Adhesive for Tough Plastic Bonds
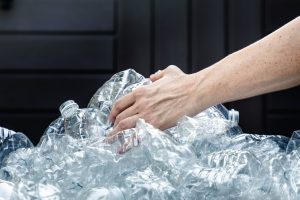
When it comes to making plastic bonds that last, picking the right adhesive is like choosing the right tool for a job. Just as you wouldn’t use a hammer to screw in a nail, you have to think about what adhesive will best suit different types of plastic. Bonds need to withstand not only the test of time but also the stresses of daily use, whether that’s for something as small as a kid’s toy or as important as a car windshield.
For plastic manufacturers in Ottawa, this decision is vitally important. Getting it right can mean stronger, more durable products—something customers will appreciate and return for. But choosing the wrong adhesive could lead to weak bonds and unhappy customers, potentially damaging a company’s reputation. So what makes an adhesive the best choice? It depends on the type of plastic you’re working with and the specific demands of the product.
Understanding Plastic Types
Plastics come with their own set of unique properties and needs. When you walk through a store, it’s easy to see just how versatile these materials are by looking at everyday items from food containers to electrical outlets. But what you don’t see is the complexity involved in gluing things like acrylic, PVC, or polycarbonate. Each type offers different strengths and limitations when it comes to bonding.
– Acrylic: Known for its transparency and strength, acrylic is commonly used for windows and display cases. But its slick surface requires an adhesive that can handle its smoothness while providing a strong hold.
– Polycarbonate: This is the tough guy of plastics, often used in safety equipment like helmets and impact-resistant windows. But bonding polycarbonate isn’t simple. It needs an adhesive that can perform in high-stress environments without cracking.
– PVC (Polyvinyl Chloride): Primarily used in plumbing and electrical applications, PVC is easy to mould but demands a specific type of adhesive that won’t corrode or weaken over time.
Understanding these types and their specific bonding needs helps in selecting the right adhesive. It’s like knowing that maple syrup pairs well with pancakes and not with pasta. Each plastic type requires careful consideration because the wrong glue can result in a bond that falls apart when you least expect it. Manufacturers rely on this knowledge to make products that are not only functional and safe but that also stand the test of time.
Types of Adhesives
Choosing the right adhesive for your plastic project can feel like choosing the best seasoning in the kitchen. Each adhesive has its own flavour, if you will. The key is to know which one works best for your needs. A brief look into different adhesives helps set the stage for successful plastic bonding.
– Cyanoacrylate (Super Glue): This one is known for its fast-setting properties, perfect for quick fixes. However, it’s not always the best choice for flexible plastics since it tends to become brittle.
– Epoxy: A versatile option that offers high strength and chemical resistance. It’s great for heavier materials but requires mixing two components and a bit of patience as it sets.
– Solvent Cement: Primarily used for bonding PVC, this adhesive actually melts the plastic surfaces together. This results in an exceptionally strong bond, making it ideal for piping and plumbing projects.
Each adhesive comes with its own pros and cons, and knowing when to use which can make a world of difference in your project. It’s like knowing when to use a whisk versus a blender in cooking.
Tips for Achieving Strong Bonds
Now that you’re familiar with various adhesives, let’s cover some practical tips to get those bonds strong and secure. Following the right techniques can often be the difference between a long-lasting bond and a temporary fix.
1. Surface Preparation:
– Clean the surfaces thoroughly to remove any dust, oil, or debris. Even a small speck can disrupt adhesion.
– Consider roughening the surface slightly using sandpaper for materials like acrylic to improve grip.
2. Correct Application Methods:
– Apply adhesive evenly. This prevents weak spots in the bond.
– Use the right amount—too much or too little can hinder performance.
3. Curing Times and Conditions:
– Give sufficient time for the adhesive to set. Whether it’s a quick-dry glue or an epoxy, rushing can compromise the bond.
– Pay attention to temperature and humidity as these can affect the setting process.
By focusing on these areas, you markedly improve the quality and durability of your plastic bonds, ensuring they meet the demands of everyday use.
Common Mistakes to Avoid
Even with a perfect choice of adhesive, simple oversights can undermine your work. Avoiding these common mistakes ensures your projects remain strong and reliable:
– Mismatching the adhesive with the plastic—double-check compatibility.
– Skipping proper surface cleaning or preparing, which leads to weaker bonds.
– Disregarding manufacturer instructions, as they often contain vital information for optimal use.
These pitfalls are common but easily avoidable. With careful planning and execution, you create robust plastic bonds that hold up to expectations.
Bringing It All Together for Ottawa’s Plastic Manufacturers
The right adhesive, careful preparation, and avoiding common mistakes go hand in hand. For manufacturers in Ottawa, integrating these practices leads to products that not only look great but also last longer. In the end, it’s all about making informed choices and paying attention to detail. By doing so, you meet customer needs and set the standard high for quality and reliability in every plastic project.
To achieve the best outcomes in your manufacturing projects, it’s crucial to choose the right adhesive and implement effective bonding techniques. For plastic manufacturers looking to enhance product durability, exploring adhesive options and addressing common challenges is essential. To optimize your adhesive use and learn more about how we can support your needs, visit Canus Plastics Inc. Discover more about how we can assist with your plastic manufacturers requirements, ensuring top-quality results for all your projects.