The Art of Plastic Welding: Techniques, Applications, and Benefits for Custom Plastic Product Manufacturing
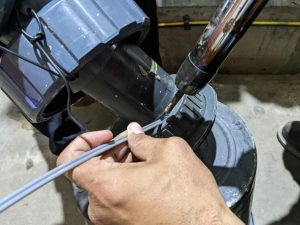
As a leader in manufacturing and selling quality plastic products in the Ottawa area, we are committed to harnessing innovative technologies and processes to deliver outstanding results. One such invaluable technique utilized in the creation of custom plastic products is plastic welding. This method involves the joining of two or more plastic parts by melting and fusing the materials, resulting in a strong and enduring bond. Plastic welding is essential for the construction of diverse products, including COVID-19 countermeasures, safety and security equipment, marketing and display cases, podiums, election boxes, windshields, tables, and benches.
In this comprehensive blog, we will explore the different plastic welding techniques utilized in custom plastic product manufacturing, each with its unique advantages and applications. We’ll discuss the benefits of plastic welding, showcasing how it can add value and quality to your custom plastic products. Additionally, we’ll highlight essential factors to consider for ensuring successful plastic welding projects, empowering you to make informed decisions and optimize your manufacturing process.
Plastic Welding Techniques and Their Applications
There are several plastic welding techniques, each with unique advantages and specific applications. We’ll explore four prominent methods and their respective benefits.
- Hot Gas Welding: This technique involves the use of heat and pressure to weld plastic parts. A specially designed hot air gun is employed to heat both the plastic pieces and the welding rod, which then melts and fuses the materials. Hot gas welding is ideal for repairing larger plastic parts like tanks or piping systems.
- Ultrasonic Welding: This process employs ultrasonic vibrations to generate heat within the plastic materials, resulting in a strong bond between them. Ultrasonic welding is best suited for joining thin-walled components, such as automotive parts and electronic housings, as well as creating watertight seals in medical devices and packaging.
- Laser Welding: This sophisticated technique uses a focused beam of light to apply heat at specific points, melting and fusing the plastic parts. Laser welding offers precision, speed, and minimal material degradation, making it suitable for small, intricate components in industries like automotive, aerospace, and medical device manufacturing.
- Friction Welding: Friction welding relies on the heat generated from the movement of two plastic components against each other. The resulting heat fuses the parts, creating a durable bond. This method is particularly advantageous when welding large, flat surfaces or cylindrical parts.
Benefits of Plastic Welding in Custom Plastic Product Manufacturing
Incorporating plastic welding techniques in custom plastic product manufacturing offers numerous benefits, including:
- Durability: Plastic welding is proven to produce resilient and long-lasting joints, ensuring the integrity and lifespan of the finished products.
- Versatility: With a variety of welding techniques available, manufacturers can choose the most suitable method for the specific application, material, and design requirements.
- Cost-Effectiveness: Plastic welding generally consumes fewer resources and requires less labor-intensive processes than mechanical fastening methods, translating to reduced production costs.
- Enhanced Aesthetics: Weld seams produced through plastic welding are often less visible than those resulting from mechanical fastening, providing a cleaner, more professional appearance.
Factors for Ensuring Successful Plastic Welding Projects
Adhering to these crucial factors can help ensure the success of your plastic welding project:
- Material Compatibility: Ensure the plastic materials being welded are chemically compatible to achieve a strong and lasting bond. It’s generally easiest to weld parts made from the same type of plastic.
- Proper Surface Preparation: Thoroughly clean and prepare the surfaces of the plastic components to be welded, as the presence of contaminants may hinder the welding process and compromise the bond strength.
- Tool and Machine Maintenance: Regularly inspect and maintain your welding equipment to ensure optimal performance, safety, and reliability during the welding process.
- Skilled Operators: Employ experienced and skilled technicians, as plastic welding requires specialized knowledge and expertise to execute effectively.
Embracing the Future of Custom Plastic Products with Plastic Welding
Plastic welding offers immense potential for the creation of exceptional custom plastic products. By understanding various techniques, their applications, benefits, and contributing factors for success, you can make informed decisions and leverage plastic welding to its fullest potential in your custom plastic product manufacturing process.
Our dedicated team of professionals at Canus Plastics Inc. is excited to support you in exploring the world of plastic welding, helping you choose the right technique, optimize your manufacturing process, and craft high-quality custom products. Contact our welders in Ottawa today to discuss your plastic welding needs and drive your manufacturing efforts to new heights.