Identifying Signs of Poor Plastic Welding and Their Fixes
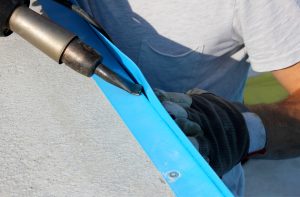
Plastic welding holds a special place in creating and repairing a wide range of products. From crafting transparent windscreens to assembling safety barriers, the technique isn’t just about joining pieces together. It’s about ensuring that each connection is solid and reliable. Poor plastic welds can lead to cracks, leaks, or pieces that simply fall apart. Recognizing these signs early on is important for maintaining the integrity and functionality of the items you depend on every day.
If you’re based in Ottawa, knowing how to notice and address these issues can save time and hassle. Welder expertise in this area ensures that fixes are done properly the first time. As you become familiar with this process, you’re better equipped to handle the practical challenges that poor welds present. Identifying these defects and knowing how fixes can be applied helps keep your plastic projects on track.
Common Signs of Poor Plastic Welding
Spotting a poor weld isn’t as hard as you might think. The first signs often show up as visual cues that something went wrong. These indicators include:
– Discolouration: A change in colour around the weld can mean too much heat was used.
– Bubbles: Trapped air during the weld process leads to bubbles that compromise the weld.
– Uneven seams: An inconsistent seam may be obvious to the naked eye.
Structural integrity issues also give away a poor weld. You might notice:
– Cracking: Stress from a bad weld leads to cracks over time.
– Weaknesses: The joint isn’t as strong as it should be, affecting the piece’s overall strength.
– Joint failure: A complete break where two pieces should be firmly joined.
Alongside these, surface imperfections can indicate trouble:
– Rough textures: Rather than feeling smooth, a rough weld could mean improper technique.
– Inconsistent lines: A wavy or jagged line along the weld suggests poor execution.
Recognizing these signs helps determine when a particular weld hasn’t done its job. Engaging with a local expert, especially in Ottawa, provides a reliable solution. Through trained eyes and skilled hands, you can fix issues with poor welds, setting your project back on course.
Causes of Poor Plastic Welds
Understanding what leads to poor plastic welds can prevent headaches down the line. The root cause often stems from three main factors: heat, contamination, and technique. First up, inadequate heat or pressure during the welding process is a common culprit. If the heat isn’t quite right, the plastic won’t merge properly, leading to weak spots and potential failures. Think of it like undercooking a cake; too little heat and it doesn’t rise as it should.
Another issue is impurities or contaminants on the surfaces being welded. Dirt, grease, or some leftover material can interfere with the welding process. This contamination acts like a barrier, preventing a strong bond. A simple example is a dirty adhesive strip; if dust gets on the sticky part, it won’t hold as firmly.
Lastly, incorrect welding techniques or improper equipment usage also contribute to faulty welds. If the welder doesn’t follow the right methods or if the equipment settings are off, the result won’t be sturdy. It’s akin to using the wrong size of a wrench on a bolt—it’s not going to tighten properly. Recognizing these causes is key to improving the outcome of welding projects.
Effective Fixes for Poor Plastic Welds
Addressing poor plastic welds requires a proactive approach. One of the most direct solutions is re-welding. This involves reheating the joint and fusing the components again, ensuring a stronger bond. However, re-welding should be done with care to avoid damaging the material. Make sure to clean the surfaces thoroughly before starting, removing any contaminants.
Surface preparation is another critical step. Clean surfaces are essential for a successful weld. You can use solvents designed for plastics to clean away any grease or grime. This simple step can make a significant difference in weld strength.
Adjusting the welding parameters can also remedy poor results. Different types of plastic require specific heat settings and pressure. Consult the material specifications to find the optimal settings. By fine-tuning these parameters, you ensure the plastic melts and bonds properly.
Ensuring Quality in Future Welding Projects
Looking ahead, establishing quality in future welding projects involves more than just fixing past mistakes. Continuous training and skill enhancement for welders is vital. This ensures that they keep up with the latest techniques and technology advancements. Regular workshops and refresher courses can keep skills sharp.
Investing in quality welding equipment and tools is equally important. High-quality tools provide more precise control and consistency, leading to better outcomes. Consider this just like using top-notch ingredients in cooking for the best results.
Implementing stringent quality control measures can also safeguard future projects. Conduct regular inspections of both the materials and the finished welds. Even minor flaws should be addressed to prevent future failures. With these strategies in place, the quality of plastic welding projects can reach new heights, minimizing the risk of defects.
Achieving Flawless Plastic Welds with Professional Help
Identifying and fixing poor welds doesn’t just prevent immediate problems; it sets a standard for excellence in your projects. Taking the time to ensure that each weld is flawless means future-proofing your work. It might seem like extra effort, but investing in quality during the initial stages can save time and resources later on.
If you’re in Ottawa and grappling with plastic welding issues, seeking expert help can make a world of difference. Professional welders have the experience and equipment to address these challenges effectively. They can provide insights you may not have considered, ensuring your projects run smoothly.
Quality welding enhances not just the durability and aesthetics of your products but also their safety and functionality. Whether you’re working on protection barriers or marketing displays, solid welds mean the end products perform as expected. By striving for high-quality welds, you maintain reliability and trust, both of which are crucial in any field. So, always aim for excellence in your plastic welding endeavors.
For anyone searching for a reliable welder in Ottawa, partnering with experts ensures your plastic welding projects are completed with precision and quality. Whether you’re tackling a new project or fixing past imperfections, Canus Plastics Inc. is ready to assist with top-notch techniques. Discover our specialized welding services and see how our expertise can elevate your work.