An In-Depth Guide to Plastic Welding Techniques
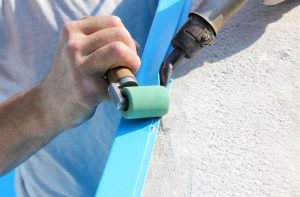
Plastic welding is a skill that is both an art and a science, combining practical knowledge with a deft touch. This craft requires an intimate understanding of materials, a careful selection of tools, and a meticulous application of technique. It’s a realm where precision and creativity meet, where the rigidity of plastic is made pliable, and the impossible is made possible.
As with any art form, mastering the intricacies of plastic welding takes time, patience, and practice. It’s an ongoing journey of discovery, where each project presents its unique set of challenges and opportunities for growth. Yet, the rewards are immense: the ability to repair, create, and innovate with a material that is ubiquitous in our daily lives.
Through this exploration, the aim is to equip you with the knowledge and confidence to master the art of plastic welding.
Popular Plastic Welding Techniques
Plastic welding processes vary in their approach to joining thermoplastic materials. Developing a comprehensive understanding of these methods is essential for determining the most suitable technique for each unique project. Let’s explore some of the most popular plastic welding techniques:
1. Hot Gas Welding
Hot gas welding, also known as hot air welding, is a versatile technique that employs a heated air stream to melt the plastic material’s surface. This process is often used for joining thermoplastics like polyvinyl chloride (PVC), polypropylene (PP), and polyethene (PE). Hot gas welding is popular in applications such as pipe welding, fabricating plastic tanks, and creating custom plastic products.
2. Ultrasonic Welding
Ultrasonic welding is a non-contact process that uses high-frequency vibrations to generate heat and fuse plastic materials. This technique is commonly used for joining thin plastic sheets or small, intricate parts. Ultrasonic welding is an ideal solution for creating products requiring precise joins, such as medical equipment, automotive components, and electronic devices.
3. Heated Tool (Butt) Welding
Heated tool welding, also known as butt welding, involves joining two plastic parts by heating their edges with a hot plate and then applying pressure. This method is particularly useful for welding thick plastic pieces and is widely employed in applications such as pipe joining and creating plastic chemical tanks.
4. Laser Welding
Laser welding uses a concentrated laser beam to generate heat and fuse plastic materials. This non-contact process offers high precision and control, making it suitable for complex and delicate plastic components. Laser welding is commonly found in medical device manufacturing, the automotive industry, and electronics production.
Applications of Plastic Welding in Manufacturing
Plastic welding plays a critical role in the manufacturing process, and its diverse techniques are utilised in various industries:
1. COVID-19 Countermeasures: Plastic welding is crucial for creating durable joints in protective barriers, face masks, and sanitiser dispensers, ensuring the products are sturdy and reliable.
2. Safety & Security: Plastic welding techniques are employed in the production of safety components such as anti-slip stair treads and safety screens, creating strong, long-lasting products that function effectively.
3. Marketing & Display Cases: Plastic welding helps to create visually appealing and robust display cases and other marketing materials to protect and showcase products in a professional, engaging manner.
4. Podiums, Election Boxes, and Furniture: Utilizing plastic welding in manufacturing processes enables the production of durable and functional products, such as podiums, election boxes, and other furniture items, ensuring their longevity and efficiency.
Tips for Successful Plastic Welding
To achieve success in plastic welding, manufacturers should adhere to several key best practices:
1. Proper Material Selection: Ensure compatibility between the materials being joined, as incompatible plastics may result in weak or failed welds.
2. Cleanliness: Thoroughly clean the surfaces to be welded, removing any contaminants that might hinder the welding process.
3. Preparing the Workpieces: Properly prepare the plastic surfaces by trimming, bevelling, or tapering them as necessary based on the chosen welding technique.
4. Temperature Control: As different plastic materials have unique melting points, maintaining precise temperature control throughout the welding process is essential to prevent overheating and distortion.
5. Skilled Operators: Invest in the training of skilled operators who understand varying plastic welding techniques and their appropriate applications, ensuring a successful outcome for each unique project.
Optimise Your Products with Expert Plastic Welding Services
Understanding the intricacies of plastic welding techniques, their applications, and best practices is essential for manufacturing durable, efficient, and high-quality plastic products. With our expert guidance and commitment to innovation, your projects will reflect the highest standards of quality and professionalism.
Reach out to our team at Canus Plastics today to discuss your plastic welding needs in Ottawa, and discover how our comprehensive solutions can elevate your product development efforts to new heights.