General Machining Safety Tips: Avoiding Common Mistakes
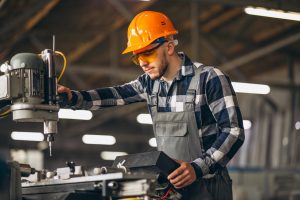
Safety in machining isn’t just about following rules—it’s about protecting people and equipment from harm. In workplaces where machinery is in constant use, even a small mistake can lead to serious accidents. It could be a minor slip like forgetting to wear gloves or something more serious like mishandling a tool. These oversights may cause injuries or damage to the equipment, leading to downtime and unexpected costs. That’s why safety measures are so important.
In Ottawa, where diverse industries rely on machining, understanding common pitfalls is essential. Plastic manufacturing companies, in particular, must remain vigilant to avoid errors that can disrupt operations. Employing robust safety protocols ensures not just compliance but smooth and efficient workflow. By examining common mistakes, we can better appreciate the vital role of safety.
Proper Training and Certification
A well-trained team is the first line of defense against accidents in the machining world. Training isn’t just a one-time event; it’s an ongoing process that keeps workers informed about the latest safety practices. Without proper training, even the most advanced machines can become a hazard. Workers who are not adequately trained may overlook crucial operational aspects, leading to mishaps.
Certification plays a crucial role in providing a structured framework for training. It offers validation that a worker has acquired the necessary skills to operate machinery safely. Many programs cover the technical aspects of machinery use, along with emergency protocols, to ensure workers know how to respond if something goes wrong. Continuous education is equally important, keeping the workforce updated on new safety technologies and methods through workshops and seminars.
Each training program should be carefully selected to meet the specific needs of the industry. For instance, a plastic manufacturing company may emphasize CNC machining safety. This ensures the training is relevant and directly applicable to daily operations. Encouraging ongoing learning creates a safer workplace environment and fosters a culture of safety.
Use of Personal Protective Equipment (PPE)
Wearing suitable personal protective equipment (PPE) can prevent countless injuries. PPE acts as a shield against potential hazards a worker might face. From minor scratches to more severe injuries, the right gear makes a difference. Common PPE items for machining include gloves, goggles, face shields, and steel-toed boots. Each piece has its purpose, such as protecting eyes from flying debris or hands from sharp edges.
Here’s a simple list to guide essential PPE in machining settings:
– Gloves: Shields hands from cuts or abrasions.
– Goggles: Protects eyes from particles and harmful substances.
– Face Shields: Offers a barrier against splashes and debris.
– Ear Plugs: Reduces noise exposure, protecting hearing over time.
– Steel-Toed Boots: Prevents foot injuries from falling objects.
Knowing how to wear PPE correctly is just as important as having it. Regular checks and maintenance of protective gear also ensure they function properly when needed. Encouraging workers to speak up if gear is uncomfortable or unsuitable can lead to improvements, ensuring everyone stays safe and comfortable on the job. Proper usage and care of PPE reflect a proactive approach to workplace safety that should be a standard in any machining environment.
Machine Maintenance and Safety Checks
Proper maintenance acts as the backbone of safe machining operations. Regular machine care prevents unexpected malfunctions, which can cause both costly repairs and hazardous situations. Machines that run smoothly are less likely to experience the breakdowns that might put workers at risk.
Organizing a schedule for maintenance checks is a smart approach to keeping machinery in optimal condition. Here’s a handy guide for what these checks could look like:
– Daily: Inspect moving parts for wear and tear, check lubrication levels, and ensure safety guards are functional.
– Weekly: Test emergency stop functions, clean key areas of dust and debris, and verify tools are stored correctly.
– Monthly: Conduct thorough inspections on electrical components, recalibrate tools if needed, and review maintenance logs for recurring issues.
Recording maintenance activities not only helps track machine health but also highlights trends that might otherwise be missed. Encouraging workers to report unusual noises or movements early can prevent bigger problems down the line. Keeping a good flow of communication ensures everyone plays a part in safety.
Proper Handling and Storage of Materials
Handling materials with care can prevent accidents and keep the workspace organized. Whether it’s raw plastic sheets or finished products, proper handling methods reduce risks and ease the workflow. Workers must handle materials in a way that minimizes strain and avoids damage.
For storing materials, clear guidelines help keep the space orderly. Storing heavy or awkward items at waist level can prevent injuries. Additionally, ensuring walkways are clear of clutter reduces trip hazards. Practicing cleanliness by regularly tidying up keeps dust and debris from accumulating, contributing to a safer and more efficient workspace.
Labeling shelves and storage areas aids in quickly finding tools and materials, saving both time and effort. This system helps avoid the chaos that can lead to mistakes. Ensuring a tidy workplace is as much about safety as it is about efficiency.
Emergency Procedures and Response
Knowing how to respond in emergencies can make a significant difference. Quick, decisive action can prevent minor incidents from escalating. Employees should be familiar with basic emergency procedures and know where to find and how to use first aid supplies.
Here’s a simple flow of steps for responding to typical emergencies like spills or electrical faults:
- Notify a supervisor or safety officer immediately.
- Clear the area of non-essential staff to prevent additional exposure.
- Act according to the facility’s emergency protocol, such as using a spill kit or cut-off switch.
- Assist in the orderly evacuation if required.
Having emergency contact numbers and a well-stocked first aid kit within easy reach is a must. Regular drills and refresher courses help workers feel prepared and confident in their ability to handle emergencies.
Safe Practices Make Perfect
Adopting comprehensive safety measures benefits both productivity and well-being. These efforts require ongoing commitment from everyone involved. By fostering a culture where safety is priority, you contribute to a more efficient and happier workplace.
Encouraging constant awareness and participation in safety practices nurtures this culture. Professional training programs not only ensure compliance but also showcase the importance of continuous learning in staying ahead of potential risks. Prioritizing safety transforms the work environment into one where efficiency and protection go hand in hand.
Promoting a culture of safety within plastic manufacturing companies is essential for maintaining a secure and productive environment. If you’re looking to enhance your understanding and implementation of safe machining practices, visit Canus Plastics Inc. to explore our comprehensive CNC machining solutions. Embrace safety-first methods and ensure your operations run smoothly with the right expertise and guidance.