Discovering the Power of Vacuum Forming for High-Quality Custom Plastic Product Manufacturing
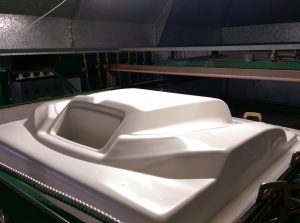
In our continuous effort to excel as a premier manufacturer and seller of quality plastic products in the Ottawa area, we recognize the importance of employing innovative technology and advanced manufacturing techniques. Among these techniques, vacuum forming plays a pivotal role, offering an efficient, cost-effective, and versatile method of crafting custom-made plastic products. Vacuum forming, a crucial component of our technological arsenal, has enabled us to cater to a broad spectrum of industries and applications, including COVID-19 countermeasures, safety and security, marketing and display cases, podiums, election boxes, windshields, tables, and benches.
Vacuum forming, also known as thermoforming, is an effective technique for producing intricate plastic objects by heating a plastic sheet until pliable, shaping it around a mold using vacuum pressure, and finally cooling it to maintain its new form. This method can be used to create large, thin-walled plastic parts and components with complex shapes while ensuring precision, consistency, and quality. Vacuum forming is particularly well-suited for the production of small to medium-sized product runs, making it an ideal solution for clients seeking customized products in relatively low quantities.
In this comprehensive blog, we will dive deep into the world of vacuum forming to uncover its process, benefits, and versatile applications across industries. We will also discuss the role of vacuum forming in overcoming manufacturing challenges, enabling companies and individuals to bring their innovative ideas to life efficiently and cost-effectively. Lastly, we will explore the various factors to consider when implementing vacuum forming for your custom plastic product manufacturing needs, ensuring exceptional results.
Demystifying the Vacuum Forming Process
The vacuum forming process is multilayered, involving a strategic combination of heat, pressure, and cooling. Let’s break down each step:
- Material Preparation: The process begins with selecting an appropriate plastic material, such as ABS or Polycarbonate, considering factors like durability, flexibility, rigidity, and heat resistance.
- Heating the Plastic: The plastic sheet is placed in an oven or infrared heater until it reaches the optimal forming temperature, making it pliable enough to be formed around the mold.
- Molding: Once heated, the plastic sheet is positioned over the mold, and vacuum pressure is applied, drawing the material tightly around the mold’s surface, ensuring precise shaping and replication of the desired form.
- Cooling: The newly molded plastic is allowed to cool and solidify, retaining its freshly acquired shape and dimensions.
- Trimming and Finishing: The final product is carefully removed from the mold, excess material is trimmed, and any necessary post-processing, such as polishing or painting, is completed.
The Many Advantages of Vacuum Forming
Vacuum forming offers numerous benefits, making it an attractive option for custom plastic product manufacturing:
- Cost-Effective Production: The vacuum forming process is more cost-efficient than other methods, such as injection molding, particularly for small to medium-sized production runs. Tooling costs, material waste, and labor expenses are generally lower, resulting in a more budget-friendly solution.
- Rapid Prototyping and Manufacturing: Vacuum forming streamlines prototyping and production, enabling the swift creation of custom plastic products. Fast turnarounds mean getting your product to market quicker, giving you a competitive edge.
- Customization and Versatility: Vacuum forming supports the fabrication of diverse plastic products, from simple to complex shapes, across industries. Its adaptiveness ensures that your ideas can be brought to life accurately and efficiently.
- High-Quality and Consistency: Vacuum forming delivers durable, consistent, and aesthetically pleasing products. The precise molding process ensures accurate replication of features and a professional finish.
Applications of Vacuum Forming Across Industries
The adaptability of vacuum forming makes it a popular choice for a broad range of industries:
- COVID-19 Countermeasures: Vacuum-formed protective barriers and personal protective equipment help create safer environments amid ongoing pandemic concerns.
- Safety and Security: Advanced security measures benefit from components molded using vacuum forming, such as housing for security cameras or access control systems.
- Marketing and Display Cases: Customized point-of-purchase displays, signage, and promotional products are efficiently created using vacuum forming, providing visually appealing and functional solutions.
- Podiums and Election Boxes: Sturdy and secure podiums for public speaking and transparent election boxes uphold the integrity of democratic processes.
- Windshields and Protective Covers: Durable, perfectly shaped windshields and protective covers offer defense against environmental elements, increasing product longevity.
Factors to Consider When Implementing Vacuum Forming
To optimize the results of your vacuum-formed plastic products, consider these crucial factors:
- Material Suitability: Selecting the appropriate plastic material for your project ensures the best compatibility with the vacuum forming process and desired final product characteristics.
- Design Complexity: The complexity of your design must be achievable with vacuum forming. Well-designed molds and attention to detail in the design stage are crucial for successful fabrication.
- Production Volume: Vacuum forming is ideal for small to medium production runs, but other methods, like injection molding, may be better suited for large-scale production.
- Skilled Workforce: A knowledgeable and experienced team is essential for executing vacuum forming projects efficiently and effectively.
Embrace the Power of Vacuum Forming for Custom Plastic Product Manufacturing
Vacuum forming offers a multitude of advantages in creating high-quality, custom plastic products efficiently and cost-effectively. Understanding the process and factors to consider can help unlock the potential of vacuum-forming technology, ensuring your products stand out in the market.
Our team of skilled professionals at Canus Plastics Inc. is dedicated to guiding you through the entire plastic vacuum forming journey, offering expert advice, insights, and best practices to achieve exceptional results in your custom plastic product manufacturing projects. Contact us today to explore how our vacuum forming expertise can help elevate your products to new levels of success.