Preventing Bubbles and Thin Spots in Thermoformed Products
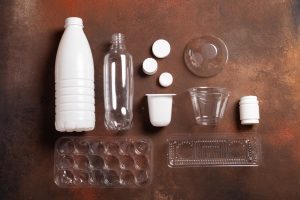
Thermoforming is a widely used method in the plastics industry, especially for making a variety of parts and products. Despite its versatility and efficiency, this process sometimes encounters two pesky issues: bubbles and thin spots. These problems are more than just minor inconveniences. They can compromise the integrity and appearance of finished products, making it crucial for manufacturers to understand and address them effectively.
Grasping the factors that lead to bubbles and thin spots can significantly improve the quality of thermoformed products. When manufacturers solve these issues, they produce pieces that meet design specifications, ensuring reliable performance and customer satisfaction. Mastering the art of preventing such defects not only leads to smoother operations but also reduces costs associated with waste and rework.
Understanding the Causes of Bubbles in Thermoformed Products
Bubbles often form during thermoforming due to several factors, with trapped air and moisture being primary culprits. When air pockets aren’t fully removed during the heating process, they expand, creating visible bubbles on the product surface. Similarly, moisture trapped in the plastic can vaporize into bubbles when heated.
There are additional factors to consider as well:
– Uneven Heating and Cooling: If the material isn’t uniformly heated, some areas might expand differently, leading to bubble formation. Proper control of heating rates and consistent cooling are essential to avoid this.
– Material Handling: Storing materials improperly before forming can introduce moisture. Handling materials with care and ensuring they are dry before use can prevent many bubble problems.
Addressing these causes is key to avoiding bubbles, requiring careful attention to both material condition and process parameters.
Preventing Thin Spots in Thermoformed Products
Thin spots are another concern during thermoforming. They typically occur when the material stretches too much in certain areas, usually due to uneven thickness or inconsistent distribution of heat during forming.
To tackle this issue:
– Consistent Material Thickness: Ensuring the raw material starts with uniform thickness can significantly help. Variations in thickness can lead to parts being unevenly formed, resulting in thin spots.
– Even Heat Distribution: Maintaining an even temperature across the material surface is essential. This ensures that the material flows and stretches consistently during forming, preventing thin areas.
– Proper Mould Design: A well-designed mould supports the material properly and guides it during shaping. Structured mould designs reduce the risk of spot thinning by controlling how the material forms over the mould.
Employing these strategies makes a big difference in the quality and durability of thermoformed products. Taking these steps not only enhances the final output but also streamlines the production process, leading to fewer rejections and more satisfied customers.
Best Practices for Quality Thermoforming
Achieving high-quality thermoforming involves a blend of careful preparation, consistent processes, and regular maintenance. Here are some best practices to consider:
– Material Preparation: Start with dry, clean materials to minimize moisture-related bubbles. Ensure materials are stored properly to prevent absorption of moisture. Checking material thickness before beginning can also set you up for success by identifying potential problems early.
– Uniform Heating and Cooling: Use controlled heating methods to achieve even material temperatures. This helps maintain uniformity and prevent both bubbles and thin spots. Regularly calibrate your equipment to ensure it provides consistent heat distribution. Cooling also matters, and ensuring a uniform rate can solidify the piece properly without stress.
– Equipment Maintenance: Routine maintenance of equipment secures consistent performance and minimizes unexpected problems during the forming process. Regular inspections help catch issues like damaged moulds or uneven heating elements before they affect product quality. Keep a maintenance schedule and document any adjustments or repairs for future reference.
Attention to these practices fosters improvements in product integrity and appearance, making the thermoforming process smoother and more predictable.
Troubleshooting Common Thermoforming Issues
Even with great preparation, thermoforming sometimes throws a curveball. Here’s how to troubleshoot common problems:
1. Identify the Problem: Start by examining your thermoformed product closely. Is there a specific area where bubbles tend to form? Or a recurring thin spot? Pinpointing where and when these issues appear helps track down their cause.
2. Check Equipment Settings: Verify that heat settings are correct and consistently applied. Sometimes, small adjustments in temperature settings or timing can resolve large issues. Ensure that heating elements are fully functional and calibrated.
3. Consider Material Quality: Low-quality or inconsistent materials can introduce unforeseen challenges. Use high-quality materials and verify that they meet specified standards. Switching to a trusted supplier or revisiting material specifications can provide solutions.
4. Seek Expert Advice: If persistent problems arise, it may be necessary to consult with professionals. Their experience often provides insights that can’t be easily gleaned from troubleshooting manuals. Don’t hesitate to reach out to a knowledgeable expert to get your process back on track.
Ensuring High-Quality Thermoformed Products
The effort invested in preventing bubbles and thin spots pays off with higher quality, reliability, and aesthetic appeal in thermoformed products. Emphasizing regular maintenance and adhering to best practices are core components that safeguard the production process.
Ultimately, staying informed and proactive about the thermoforming process enables manufacturers to produce dependable, high-quality products. The right preparations and timely troubleshooting ensure that your operations can withstand unexpected challenges, all while maintaining the standard of excellence that defines top tier production.
To enhance your production capabilities and ensure the highest quality in your thermoforming projects, discover how Canus Plastics Inc. can support your needs as plastic manufacturers. Our expertise in innovative solutions can help streamline your processes and deliver results that meet the exacting standards of your industry.