Understanding Adhesives: Types We Use in Plastic Assembly
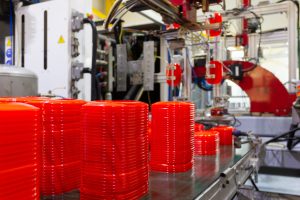
At Canus Plastics Inc., we pay meticulous attention to every detail in our manufacturing processes, understanding that the smallest components can significantly influence the overall quality and functionality of our products. One of the critical factors that play a pivotal role in the assembly of our plastic products is the selection and application of appropriate adhesives. Adhesives are not just about sticking two surfaces together; they are about creating a bond that enhances the durability, aesthetics, and performance of the final product.
Our extensive use of adhesives spans across various projects, where we tailor adhesive choices to specific materials and design requirements. This ensures not only a strong bond but also compatibility with the physical and chemical properties of the components involved. By carefully selecting and applying these adhesives, we maintain high standards of quality and reliability in our product offerings, from intricate components for COVID-19 countermeasures to sturdy, visually appealing marketing display cases.
Moreover, our expertise allows us to innovate continually. By harnessing the latest advancements in adhesive technology, we enhance our manufacturing processes, leading to faster production times, reduced costs, and improved product longevity. The consequents benefits to our customers are clear — superior plastic products that meet their precise needs in various industries, including safety and security, automotive, and consumer goods.
What Are Adhesives and How Do They Work in Plastic Assembly?
At Canus Plastics Inc., we often leverage the unique properties of adhesives to enhance the durability and functionality of our plastic products. Adhesives are substances applied to one or both surfaces of two separate items that bind them together and resist their separation. In the context of plastic assembly, we use adhesives to join parts without the need for mechanical fasteners, which can reduce the integrity and appearance of the finished products.
The process involves choosing the right adhesive based on the material’s properties and the required strength of the bond. Once applied, the adhesive undergoes a curing process, where it solidifies to form a firm, lasting bond. This is crucial in many of our productions, from marketing display cases to security barriers, where the strength of the bond contributes to the overall quality and safety of the product.
Types of Adhesives We Use and Their Specific Applications
In our manufacturing processes at Canus Plastics Inc., we employ a variety of adhesives, each selected for its particular advantages depending on the product application. Here are some common types of adhesives we use:
- Acrylic Adhesives: Known for their excellent weather resistance and strength, acrylic adhesives are perfect for outdoor products like election boxes or safety barriers. These adhesives provide a strong bond that does not weaken under sunlight or weather changes.
- Epoxy Adhesives: Used for their high strength and durability, epoxies are ideal for products requiring a particularly robust bond. Their superior chemical and heat resistance makes them suitable for components of COVID-19 countermeasures where sterilization might be frequent.
- Polyurethane Adhesives: With their flexibility and strong bonding capabilities, polyurethane adhesives are a choice for items that may experience impacts or need to absorb shocks, such as certain parts of windshields and tables.
- Silicone Adhesives: These are used where flexibility along with heat resistance is necessary. Silicone adhesives work well in pods and marketing display cases where a durable yet slightly flexible bond is needed.
Each type plays a pivotal role in ensuring that the components we assemble stand up to the rigors of their intended use, while also preserving the aesthetic qualities of the product. By understanding and applying different adhesives correctly, we enhance both the functionality and the longevity of our plastic products.
The Benefits of Using Advanced Adhesives in Plastic Manufacturing
In the realm of plastic manufacturing, the strategic use of advanced adhesives underpins many of our most critical processes. At Canus Plastics Inc., we recognize that integrating high-quality adhesives enhances not only the integrity but also the precision of every product we create. One significant benefit is the uniform stress distribution within the joints of materials, which mitigates potential weaknesses that might be introduced using other fastening methods like welding or bolting. This ensures that products like windshields and podiums retain structural strength and longevity.
Moreover, the aesthetic value provided by adhesives cannot be overstated. Unlike mechanical fasteners, adhesives offer a seamless look, essential for high-quality display cases and marketing materials that play a crucial role in brand representation. Additionally, the lightweight nature of adhesives contributes to maintaining the overall lightness of products, an invaluable asset in manufacturing items like portable election boxes and COVID-19 countermeasures that are frequently moved and repositioned.
Best Practices for Applying Adhesives in Plastic Assembly
To harness the full potential of adhesives in our manufacturing processes, we follow a series of best practices that ensure optimal results. First and foremost, surface preparation is crucial. We meticulously clean and, if necessary, activate all surfaces to be bonded. This ensures that contaminants such as oils or dust do not compromise the bond’s integrity. Choosing the right adhesive for the specific material and application is next: a step that requires deep knowledge of the chemicals’ properties and the stresses the product will endure.
Proper application techniques are also critical – applying the correct amount of adhesive promotes strong, durable bonds and reduces waste. Moreover, controlling the environment during application—like humidity and temperature—can significantly influence the curing process and effectiveness of the adhesive. Through these practices, we ensure that the adhesives work exactly as needed, reinforcing the reliability and durability of our products.
Concluding Reflections
In every piece we create at Canus Plastics Inc., from the smallest component in a COVID-19 shield to the largest marketing display, adhesives play a pivotal role. They not only enhance the durability and functionality of the products but also contribute to aesthetic perfection and environmental responsibility. As we continue to explore and integrate advanced adhesive technologies, we remain committed to delivering products that meet the highest standards of quality and innovation.
If you’re looking to enhance your project with high-quality, precision-crafted plastic components, consider how advanced adhesives utilized by Canus Plastics Inc. can contribute to your success. Contact us today to discuss how we can bring your vision to life with our expert assembly and adhesive application capabilities.