Vacuum Forming: Turning Plastic Sheets into Useful Objects
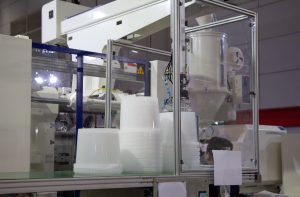
Vacuum forming is a cool way to shape plastic sheets into lots of useful things we use every day. This technique involves heating a plastic sheet until it’s soft and then stretching it over a mould where a vacuum sucks out the air, causing the plastic to fit snugly over the mould. This simple yet effective process can create detailed and durable items quickly.
This technique is popular because it allows for making a wide range of products, from packaging materials to automotive parts and household items. It’s an efficient solution for creating lightweight and sturdy products which are often less expensive than those made with other methods.
By understanding how vacuum forming works, we appreciate the role it plays in creating many of the plastic products we rely on. It’s a fascinating process that combines science and creativity, transforming flat sheets into three-dimensional objects that meet various needs. Let’s explore how this process works, its applications, and the key benefits it offers in making various products.
Understanding Vacuum Forming and Its Process
Vacuum forming is a handy technique used to shape plastic into various forms. The process begins by heating a plastic sheet until it becomes soft and pliable, usually using a special oven. Once the plastic sheet reaches the right temperature, it’s stretched over a mould. The mould is a pre-shaped object that gives the plastic its new form.
Once the softened plastic sheet is draped over the mould, a vacuum is applied. This vacuum sucks out the air between the mould and the plastic sheet, making the plastic snugly fit the mould’s shape. This creates precise and detailed features, which is especially useful in manufacturing custom parts and products. It’s a method that’s quick and effective, allowing for the mass production of items that are both complex and simple.
Some important parts of the vacuum forming process include:
– Heating: Getting the plastic to the right temperature without burning it.
– Moulding: Using moulds made from various materials like wood, metal, or resin, depending on the detail and durability needed.
– Cooling: Letting the plastic harden before removing it from the mould.
The equipment setup can vary depending on the size and detail of the items being produced. Large products require big machines, while smaller items can be made using simple tabletop equipment. This scalability is one of vacuum forming’s biggest strengths.
Common Products Made Through Vacuum Forming
Vacuum forming helps create a wide array of everyday items across different industries. This method is popular for its efficiency and cost-effectiveness, making it ideal for both small-scale and large-scale production. Let’s explore some common products made using vacuum forming.
1. Packaging: One of the most widespread uses is in packaging. Clamshell packaging, blister packs, and plastic trays are all made using vacuum forming. These products are essential in the food, medical, and retail industries for protecting and displaying goods.
2. Automotive Parts: Vacuum forming produces car parts like dashboards, door panels, and interior trim. These parts are lightweight and durable, perfect for vehicles that need to be economical and stylish.
3. Household Items: Everyday items like plastic containers, bins, and trays often come from vacuum forming. Their durability and design flexibility make them a staple in homes.
4. Display and Signage: From store displays to large advertising signs, vacuum forming creates sturdy and visually striking products. This helps businesses attract customers and convey messages effectively.
5. Medical Equipment: Custom trays and casings for medical devices are crafted with vacuum forming, ensuring clean, safe, and precise containment solutions.
These examples show how versatile vacuum forming is, catering to various needs across many sectors. It’s not restricted to a specific industry, allowing designers and manufacturers to explore and produce a variety of products. This versatility ensures that vacuum forming remains a popular choice for creating reliable and innovative products.
Advantages of Using Vacuum Forming for Manufacturing
Vacuum forming offers key benefits that make it a preferred choice in manufacturing processes. One of its primary advantages is cost-effectiveness. By using straightforward tools and equipment, businesses can reduce production expenses while maintaining high output levels. This makes vacuum forming an attractive option for creating large quantities of items without breaking the bank.
Another benefit is the flexibility of design. Vacuum forming allows for easy customization, letting manufacturers create detailed and complex shapes. This design adaptability is perfect for making unique or precise products across various industries, from simple trays to intricate automotive parts.
The process is also relatively quick, thanks to its efficient cycle times. Manufacturers can produce items swiftly, accelerating time-to-market and keeping up with demand. This agility can be a game-changer, especially in competitive industries where speed and efficiency are crucial.
Here’s a quick summary of the advantages:
– Cost-Effective: Lower production costs with efficient materials and equipment use.
– Flexible Design: Ability to create diverse and detailed shapes easily.
– Quick Production: Faster cycle times increase efficiency.
– High Quality: Consistent production ensures reliable and sturdy products.
These advantages demonstrate why vacuum forming continues to be a valuable tool in a wide range of sectors.
The Role of Vacuum Forming in Creating Canus Plastics Products
Vacuum forming plays a significant role in the diverse range of products offered by Canus Plastics Inc. One of its key contributions is in producing COVID-19 countermeasures. By using vacuum forming, Canus Plastics can efficiently create protective barriers and shields, ensuring safety in various environments. These essential products are both durable and customizable, ideal for widespread use.
In the realm of safety and security, vacuum forming allows for the creation of sturdy and reliable items. Products like election boxes and podiums require precision and durability, and vacuum forming delivers both. These items are essential for public settings, where they need to stand up to frequent use and provide trustworthy service.
For marketing and display purposes, vacuum forming hits the mark as well. Display cases and stands crafted through this method not only look professional but also provide structural integrity. This ensures products are showcased attractively while remaining secure.
Here’s how vacuum forming helps Canus Plastics:
– COVID-19 Countermeasures: Efficient production of protective barriers.
– Safety & Security: Durable and precise election boxes, podiums, and more.
– Marketing & Display: Attractive and sturdy cases and stands.
Through vacuum forming, Canus Plastics can offer an array of products that match client needs while maintaining quality and adaptability.
Conclusion
Vacuum forming stands out as an invaluable process in modern manufacturing, providing solutions across numerous fields such as safety, security, and marketing. Its cost-effectiveness and ability to create detailed designs make it an ideal choice for producing high-quality products. By transforming plastic into vital everyday objects, vacuum forming meets diverse needs with precision and reliability.
The adaptability of vacuum forming in producing various items, from protective gear to elegant display cases, underscores its essential role in manufacturing. With its ability to ensure that custom designs are economically feasible and swiftly available, vacuum forming aligns perfectly with the demands of rapid production and quality assurance.
For companies such as Canus Plastics Inc., vacuum forming is integral to crafting solutions that cater to market demands efficiently. As technology advances, the continued evolution of vacuum forming will likely enhance its impact and expand its reach into new areas of production.
Canus Plastics Inc. is here to meet your needs with our expertly engineered plastic vacuum forming products. Whether you’re looking for precise solutions or innovative designs, we deliver quality and reliability you can trust. Contact us today to explore how we can assist you in transforming ideas into reality with our skilled manufacturing processes.