An In-Depth Look at Thermoforming in Plastic Manufacturing: Processes, Advantages, and Applications
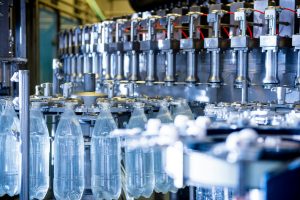
In the world of plastic manufacturing, diverse techniques and processes are employed to create high-quality products that serve various purposes. Each technique and technology offers unique advantages and applications, including CNC machining, vacuum forming, thermoforming, general machining, polishing, welding, adhesives, and assembly. At Canus Plastics Inc., we are devoted to providing superior plastic manufacturing solutions to our clients, and our extensive expertise in these processes and technologies backs us.
Thermoforming is a plastic forming process in which a heated plastic sheet is moulded into the desired shape using pressure and/or vacuum. Once the desired shape has been achieved, the plastic is cooled down and trimmed. Thermoforming is commonly employed in producing a wide variety of plastic products, including COVID-19 countermeasures, safety and security equipment, marketing and display cases, podiums, election boxes, windshields, tables, and benches, among others.
In this guide, we aim to provide a thorough understanding of the thermoforming process, its advantages, and its applications across different industries. By gaining a solid grasp of thermoforming’s capabilities, you can make informed decisions for your plastic manufacturing requirements and create innovative, high-quality products that cater to the needs of your respective industry.
Understanding the Different Thermoforming Processes
Thermoforming offers various processes that cater to different applications, product requirements, and design specifications. These processes share the fundamental step of heating plastic sheets, but they differ in the way the sheets are transformed into the desired shape:
1. Vacuum Forming
Vacuum forming involves heating a plastic sheet and placing it over a mould. A vacuum is then applied to eliminate air between the sheet and the mould, causing the plastic to conform to the mold’s shape. This process is suitable for creating products that do not require intricate detailing or precise tolerances, and it is primarily used for producing large, shallow objects with a relatively simple design.
2. Pressure Forming
Pressure forming follows a similar method to vacuum forming but uses air pressure instead of a vacuum to force the heated plastic sheet onto the mold. This process enables a higher level of detail and more precise tolerances when compared to vacuum forming. Pressure forming is well-suited for creating products with complex geometries and fine surface textures.
3. Drape Forming
In drape forming, the heated plastic sheet is manually or mechanically draped over the mold, relying on gravity to shape the material. This process provides a quick and cost-effective way to produce small quantities of simple products, as it usually does not require specialized equipment or complex tooling.
4. Twin Sheet Thermoforming
Twin sheet thermoforming is an advanced process that involves heating two separate plastic sheets and forming them simultaneously. The sheets are either vacuum or pressure formed onto corresponding male and female moulds, and they merge together during the cooling process, resulting in a single hollow product with a seamless bond. This method is ideal for creating double-wall products and complex, multi-component assemblies.
Delving into the Advantages of Thermoforming
Thermoforming as a plastic manufacturing technique offers several advantages over alternative methods:
1. Reduced Tooling Costs
Compared to injection moulding, thermoforming typically has lower tooling costs due to the simplicity of the moulds, which are generally made from temperature-resistant materials such as aluminum. This makes thermoforming an attractive option for small to medium production runs and rapid prototyping.
2. Shorter Lead Times
Thermoforming moulds can be designed and fabricated quickly, offering significantly shorter lead times than other processes like injection moulding. Quicker production translates to faster product development, allowing you to respond to market demands more efficiently.
3. Design Flexibility
Thermoforming permits the use of a wide range of plastic materials and thicknesses, enabling designers to achieve a broad array of design specifications, such as transparency, impact resistance, and UV stability. This flexibility allows you to create products that are tailor-made for their intended application.
4. Material Efficiency
Since thermoforming involves heating sheets of plastic and then trimming the excess material once the product is formed, there is minimal waste of material. Additionally, the excess material can often be recycled and reused, contributing to a more eco-friendly manufacturing process.
Exploring Thermoforming Applications Across Industries
The thermoforming process’s adaptability and efficiency have led to its widespread use in various sectors:
1. COVID-19 Countermeasures: Thermoforming is utilized in the production of protective face shields, plastic barriers, and other equipment to help curb the spread of the virus and ensure public safety.
2. Safety & Security: Thermoformed products such as safety equipment housings and tamper-resistant enclosures ensure the durability and reliability needed in these critical applications.
3. Marketing & Display Cases: Thermoforming creates visually appealing and lightweight display cases, signages, and promotional materials that catch the attention of potential customers and clients.
4. Automotive & Transportation: The automotive industry frequently utilizes thermoformed components such as vehicle interiors, bumpers, and windshields due to the process’s ability to create complex shapes with precise tolerances.
Tips for Successful Thermoforming Projects
Here are some best practices to help ensure your thermoforming project’s success:
1. Material Selection: Choose the appropriate plastic material for your product based on its specific design requirements and intended use.
2. Partner with Experts: Work with experienced thermoforming professionals who can provide guidance and support throughout the design and production processes.
3. Optimize Mold Design: Collaborate closely with your thermoforming partner to optimize the mould design, ensuring efficient and accurate product formation.
Embrace the Power of Thermoforming for Your Plastic Manufacturing Projects
By understanding thermoforming’s processes, advantages, and applications, you can make informed decisions for your manufacturing projects and capitalize on this versatile technique to produce innovative, high-quality products tailored to your industry’s needs.
At our company, we are dedicated to delivering outstanding thermoforming solutions backed by our expert knowledge and commitment to excellence. Contact our plastics suppliers at Canus Plastics Inc. today to discuss your thermoforming requirements and discover how we can collaborate to bring your ideas to life and create exceptional results for your plastic manufacturing needs.