A Comprehensive Guide to Plastic Welding Techniques and Applications
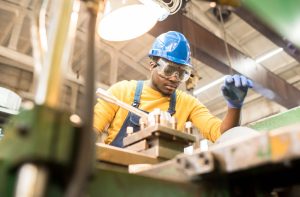
In the ever-evolving plastic manufacturing industry, a wide range of techniques and processes are employed to create a diverse array of products and applications. As a provider of high-quality plastic products in the Ottawa area, we rely on our extensive expertise in technologies like CNC machining, vacuum forming, thermoforming, general machining, polishing, adhesives, and assembly to deliver unparalleled results for our clients. One essential aspect of plastic fabrication is plastic welding – a method of joining plastic materials to create strong, durable, and dependable connections.
Plastic welding’s versatile applications span numerous industries, including COVID-19 countermeasures, safety and security products, marketing and display cases, podiums, election boxes, windshields, tables, and benches. Mastering the art of plastic welding allows for the creation of high-performance products that both meet and exceed the expectations of their intended audience.
In this in-depth blog post, we will explore various plastic welding techniques, uncovering their unique advantages, drawbacks, and ideal applications. This comprehensive guide will not only enable you to make informed decisions on the most suitable technique for your specific project requirements but also empower you to create virtually seamless connections between plastic components, ensuring long-lasting reliability and durability.
By the end of this article, you will have gained valuable insight into the different plastic welding methods available, their respective applications, and the factors to consider when selecting the ideal technique for your plastic manufacturing project. Join us in this informative journey through the world of plastic welding and acquire the knowledge and confidence needed to succeed in the realm of plastic fabrication.
1. Hot Gas Welding
Hot gas welding, also known as hot air welding, involves using a stream of hot air or gas to melt the edges of the plastic materials being joined. A filler material, typically a rod made of the same material as the pieces being welded, is often used to reinforce the joint. This method is suitable for a wide range of thermoplastic materials, including PVC, polypropylene, and polyethylene.
2. Extrusion Welding
Extrusion welding, a variation of hot gas welding, utilizes an extruder that heats and plasticizes a filler material and then extrudes it through a nozzle to create a consistent bead of molten plastic. This molten plastic is applied to the joint area, fusing the materials together. Often used in industrial applications, extrusion welding is highly effective for joining large, flat surfaces and fabricating products like water tanks and containment linings.
3. Ultrasonic Welding
In this technique, high-frequency vibrations are emitted from an ultrasonic horn and transmitted through the plastic materials, generating heat from the friction between the two surfaces. This heat melts the materials and allows them to bond, creating a strong joint without the need for additional heat sources or adhesives. Ultrasonic welding is particularly suitable for small, intricate parts and high-volume production, commonly found in the electronics and automotive industries.
4. Laser Welding
Laser welding involves the use of a high-energy laser beam to melt the plastic materials, allowing for a clean and precise bond. This method is ideal for joining complex or intricate shapes and sealing intricate channels. Laser welding is commonly used in the medical and electronics industries, where precision and repeatability are crucial.
Understanding the Advantages and Limitations
Each welding method offers its unique set of advantages and limitations, making it important to understand these aspects before selecting the most appropriate technique for a given plastic fabrication project:
- Hot Gas Welding: This method is highly versatile, cost-effective, and easy to learn. However, it also entails a longer processing time and is largely dependent on the welder’s skill level, leading to potential inconsistencies in the final result.
- Extrusion Welding: Known for its strong, water-tight joints and efficient use of filler material, extrusion welding is effective for large-scale applications. On the downside, it may not be suitable for intricate or small-scale products due to the equipment’s size and inaccessibility to certain joint angles.
- Ultrasonic Welding: With fast processing times, high repeatability, and energy efficiency, ultrasonic welding is excellent for precision applications. However, it is limited by the size and thickness of the materials, and equipment costs can be comparatively high.
- Laser Welding: Laser welding’s advantages include precision, versatility, and a fast processing time with no additional filler material requirements. The limitations include higher equipment costs, safety requirements, and potential material restrictions due to transparency and laser absorption.
Selecting the Right Technique for Your Application
When selecting the appropriate plastic welding technique for your project, consider the following factors:
- Material Compatibility: Ensure that the chosen method is compatible with the plastic materials you intend to join.
- Production Requirements: Consider the scale and complexity of the project, as well as the required speed and efficiency of the welding process.
- Geometric Constraints: Evaluate the size, shape, and intricacy of the parts being joined and select a technique that accommodates these geometric factors.
- Welding Precision: If high precision and repeatability are crucial for your application, opt for a method like ultrasonic or laser welding.
Mastering Plastic Welding for Exceptional Results
The art of plastic welding plays an integral role in the successful fabrication of plastic products for a wide range of applications and industries. By understanding the nuances of each welding technique and carefully selecting the best method, you can achieve superior product quality, durability, and performance.
At our company, our knowledgeable team of plastic fabrication experts is ready to assist you in selecting the ideal plastic welding technique for your project. Reach out to our plastic fabrication company today to discuss your requirements and discover how our commitment to excellence can help bring your vision to life and ensure outstanding results for your plastic manufacturing needs.