Maximizing Efficiency with CNC Machining in Plastic Fabrication
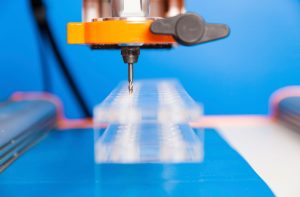
In the realm of plastic fabrication, technological advancements have paved the way for new and innovative methods to create high-quality, specialized products. The incorporation of computer-aided design and manufacturing systems, such as CNC machining, has revolutionized the manufacturing process, streamlining production and increasing overall efficiency. As a leading provider of quality plastic products in the Ottawa area, we constantly explore new ways to foster innovation and continue delivering unparalleled results to our clients across a wide range of industries and applications.
In this comprehensive blog post, we will delve into the world of CNC machining and its applications in plastic fabrication. We will highlight the distinct advantages of this cutting-edge technology, explore various machining techniques, as well as discuss critical factors to consider when employing CNC machining for plastic fabrication projects. Join us as we uncover the full potential of utilizing CNC machining in the plastic manufacturing process, and learn how this technology can enhance your project’s outcome and contribute to overall success.
Advantages of CNC Machining in Plastic Fabrication
CNC machining offers a range of distinct advantages when applied to plastic fabrication, setting itself apart from conventional methods to benefit a broad spectrum of projects:
- Precision: With the use of sophisticated software to direct cutting tools, CNC machining allows for the consistently accurate production of intricate, complex parts. This advantage is vital for industries that demand dimensional accuracy and repeatability.
- Efficiency: CNC machines are capable of operating around the clock, often with minimal human intervention or downtime. This ability results in reduced lead times and faster turnaround for projects.
- Flexibility: CNC machining can handle a diverse array of designs and materials, catering to unique project requirements without the need for manual adjustments or customized tooling.
- Cost-Effectiveness: While the initial investment for CNC machines may be high, the production efficiency and reduced labor costs can contribute to long-term cost savings.
Popular CNC Machining Techniques for Plastic Fabrication
CNC machining encompasses a variety of techniques, each suited for specific plastic fabrication projects. Some of the most widely used methods include:
- CNC Milling: This technique employs a rotating cutting tool to remove material from a plastic workpiece. CNC milling is versatile and capable of producing complex, multi-axis forms, making it suitable for a wide range of applications.
- CNC Turning: CNC turning uses a stationary cutting tool to remove material as the workpiece rotates on a spindle. This method is ideal for creating cylindrical or conical shapes with a high degree of accuracy and repeatability.
- CNC Routing: CNC routers use a high-speed cutting tool to carve out intricate designs or to cut larger plastic sheets into precise shapes. This versatile technique is well-suited for producing detailed, artistic components, such as marketing and display cases, as well as larger parts.
- CNC Drilling: Using a rotating drill bit, CNC drilling creates accurate holes in plastic materials with precise depth control, facilitating the assembly process of complex plastic components.
Factors to Consider When Choosing CNC Machining Techniques
To optimize the efficiency and cost-effectiveness of CNC machining in plastic fabrication, consider the following aspects:
- Material Compatibility: Ensure the chosen CNC machining technique is compatible with the specific plastic material being used in your project.
- Tolerances and Geometries: Evaluate the required dimensional tolerances and complexities of the component and select a CNC machining method that can accommodate these specifications.
- Production Volume: Assess the production scale – CNC machining is ideal for low-to-medium volume production, while techniques like vacuum forming and thermoforming are better suited for high-volume projects.
- Finishing Requirements: Some CNC machining techniques may require additional post-processing, such as polishing or deburring, to achieve the desired finish quality. Consider these finishing steps when planning your plastic fabrication project.
Real-World Applications of CNC Machining in Plastic Fabrication
CNC machining has proven itself invaluable in various industries thanks to its ability to manufacture precision components efficiently. Some notable applications include:
- COVID-19 Countermeasures: CNC machining has been a critical player in the rapid development and production of components for medical equipment, such as ventilator parts and face shield frames.
- Safety and Security: CNC machines can produce plastic parts for security cameras, access control systems, and other safety equipment, requiring consistent quality and accuracy.
- Election Boxes and Podiums: The flexibility and precision of CNC machining enable the creation of secure, custom election boxes and visually appealing podiums with intricate designs and branding elements.
- Automotive and Aerospace: With a strong demand for lightweight, high-strength components, CNC machining plays a crucial role in producing parts for the automotive and aerospace industries, such as plastic enclosures, brackets, and panels.
Embracing CNC Machining for Plastic Fabrication Excellence
CNC machining has established itself as an integral part of the plastic fabrication process, offering unparalleled advantages in precision, efficiency, and versatility. By understanding the capabilities of each CNC machining technique and selecting the most appropriate method for your project, you can ensure a successful outcome that meets your quality, cost, and timeline expectations.
Our skilled team of plastic fabrication experts is ready to assist you in making the best use of CNC machining for your next project. Reach out to us today at Canus Plastics Inc., and let us help you unlock the full potential of CNC machining in plastic fabrication, leading to exceptional results for your unique applications.