An Overview of Adhesives in Plastic Manufacturing: Strength, Versatility, and Application
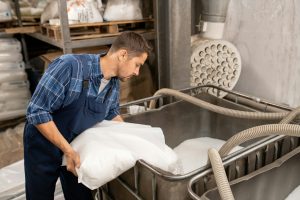
As a reliable plastic product manufacturer in the Ottawa area, we take pride in providing a comprehensive range of plastic manufacturing services, including CNC machining, vacuum forming, thermoforming, general machining, polishing, welding, adhesives, and assembly. In this article, we will explore the critical role of adhesives in plastic manufacturing and how they contribute to creating robust and versatile bonds for various products and applications.
Adhesives are integral to many aspects of plastic manufacturing, offering a reliable alternative to traditional joining methods such as mechanical fasteners, welding, and thermal bonding. They provide several advantages, including uniform stress distribution, corrosion resistance, and the ability to bond different materials. Adhesives are paramount to delivering outstanding quality, durability, and performance in numerous applications, including safety and security products, marketing and display cases, COVID-19 countermeasures, podiums, election boxes, windshields, tables, and benches.
Understanding different adhesive types, their unique characteristics, and suitable applications is crucial to selecting the best bonding solution for your project. Join us as we delve into various adhesives widely used in the plastic manufacturing industry, their strengths and limitations, and recommendations for achieving optimal results. If you’re looking for expert guidance for your next plastic manufacturing project, our team at Canus Plastics is here to help you navigate the complex world of adhesives, ensuring your products meet the highest standards of quality and performance.
Exploring Different Types of Adhesives
There is a wide range of adhesives utilized in the plastic manufacturing industry, each with its unique bonding capabilities and characteristics. Let us examine some of the most popular adhesive types and their respective performance attributes:
1. Cyanoacrylate Adhesives (Super Glue)
Cyanoacrylate adhesives, commonly known as super glue, are fast-setting adhesives that provide strong bonding in just a few seconds. They offer excellent adhesion to various materials like plastics, metals, ceramics, and rubber. Some benefits of cyanoacrylate adhesives include rapid cure time, high bond strength, and excellent resistance to temperature and humidity.
2. Epoxy Adhesives
Epoxy adhesives are two-component systems consisting of a resin and a hardener, which, when combined, form a robust, rigid bond. Epoxies offer excellent adhesion to various materials, including plastics, metals, wood, and concrete. Key advantages of epoxy adhesives are their high bond strength, chemical resistance, and durability. They are suitable for bonding dissimilar materials and are often used in structural applications.
3. Polyurethane Adhesives
Polyurethane adhesives are versatile, single or two-component materials that provide flexible, yet robust bonds. They are compatible with a wide range of substrates, including thermoplastics, metals, and wood. Polyurethane adhesives offer excellent impact resistance, high load-bearing capability, and resistance to temperature fluctuations and weathering.
4. Acrylic Adhesives
Acrylic adhesives provide high-strength bonds and are known for their adhesion to difficult-to-bond materials, such as low surface energy plastics. They offer good resistance to solvents, temperature variations, and UV radiation. Acrylic adhesives are available in both one and two-component systems and are often used in applications requiring long-term durability, such as automotive and outdoor applications.
Understanding Adhesive Performance Characteristics
When selecting the most suitable adhesive for your project, it’s essential to consider the following performance characteristics to ensure optimal bonding results:
- Bond Strength: The bond strength of an adhesive refers to its ability to withstand forces without separating. Different adhesives exhibit varying levels of bond strength, which should be considered based on your project’s specific requirements.
- Cure Time: Cure time varies among adhesives and affects the time required to reach full bond strength. Fast-curing adhesives may be preferred in high-speed production environments, while others may require longer cure times for optimal performance.
- Temperature and Chemical Resistance: Different adhesive types exhibit varying degrees of resistance to temperature, chemicals, and environmental factors like humidity and moisture. It is important to consider these factors when selecting an adhesive for your project.
- Flexibility: Flexible adhesives are essential for applications that require movement or expose the bond to vibration and shock. Adhesives that provide both strength and flexibility are ideal for projects that involve dynamic stress.
Adhesive Applications in Plastic Manufacturing
The use of adhesives in plastic manufacturing spans numerous industries and applications:
- Safety and Security Products: Adhesives are used to bond protective panels, security screens, and access control devices to ensure lasting durability and performance.
- Marketing and Display Cases: Adhesive bonding is crucial for assembling intricate marketing displays, signage, and product enclosures, creating seamless and visually appealing results.
- COVID-19 Countermeasures: Adhesives play a vital role in the manufacturing of plastic barriers, face shields, and other protective equipment, where strong, durable bonds are crucial for optimal functionality and safety.
- Podiums and Election Boxes: The assembly of podiums, election boxes, and voting booths often requires the use of adhesives to ensure secure, long-lasting bonds that can withstand repeated handling and transport.
Selecting the Right Adhesive for Your Project
Choosing the most suitable adhesive for your plastic manufacturing project involves assessing factors like material compatibility, bond strength requirements, environmental exposure, and desired bond flexibility. Consulting with an experienced plastic manufacturer who is well-versed in various adhesive types and their performance characteristics can provide invaluable guidance in selecting the best adhesive option for your project.
Rely on Our Expertise in Adhesives and Plastic Manufacturing
Understanding the different adhesive types, performance characteristics, and applications in plastic manufacturing enables you to make informed decisions when developing products that require robust and versatile bonding solutions. We are dedicated to providing expert advice and services in the realm of adhesives, ensuring that your projects achieve the highest standards of quality and performance. Reach out to Canus Plastics Inc., a plastic manufacturing company, today to discuss your project requirements and discover how our expertise in adhesives can help bring your plastic manufacturing projects to life.